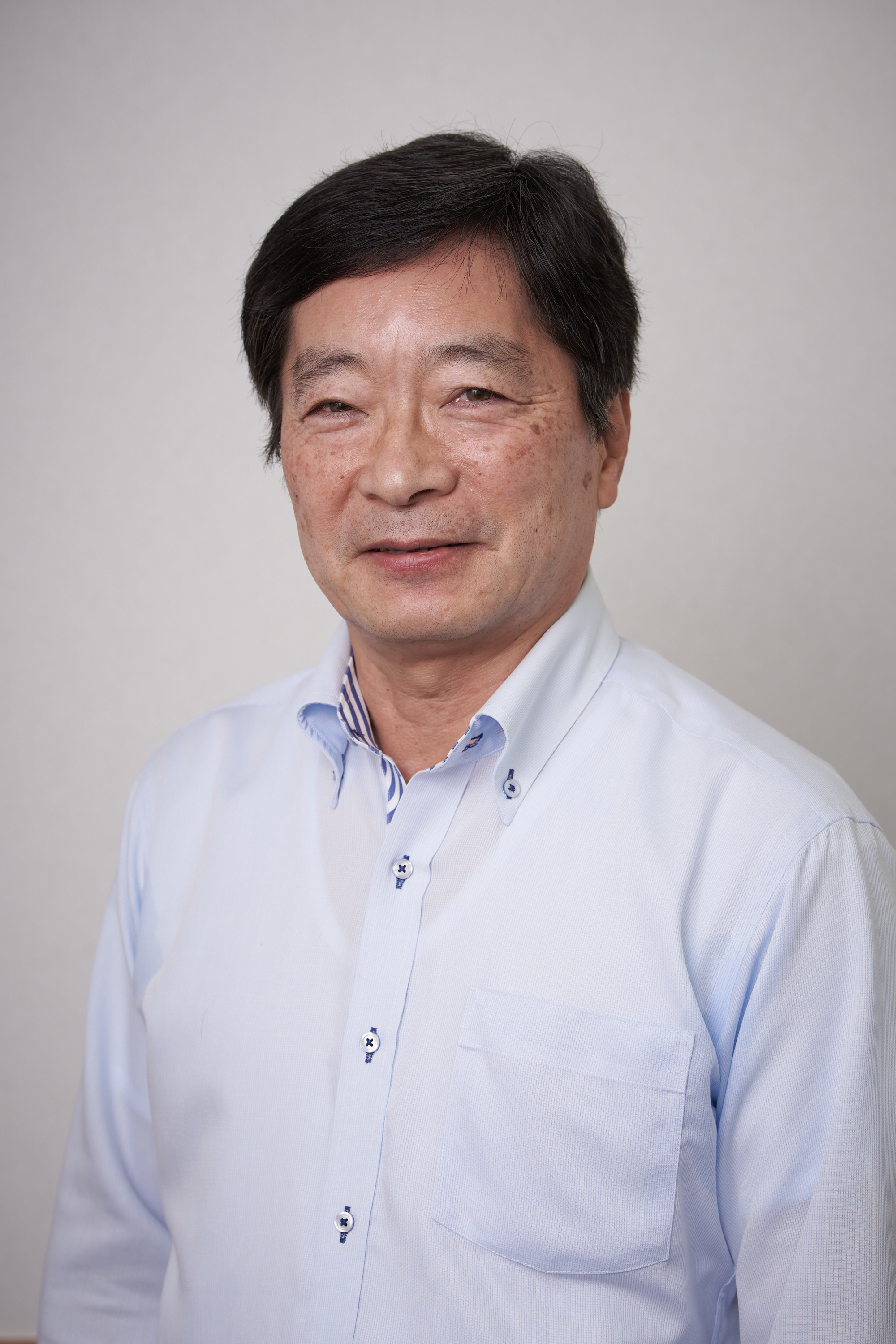
売上向上や販路拡大、顧客からの信頼獲得など、さまざまな恩恵をもたらす“業務改善”。働き方改革の影響もあり、多くの中小企業でも試みられていますが、「思うように進まない」といったケースが後を絶ちません。複雑化する現場課題が絡み合い、着手すべきポイントが明確にならないことも、原因の一つでしょう。そこで本シリーズ記事では、中小企業診断士の山田健さんに業務改善のポイントをさまざまな観点から解説していただきます。今回は倉庫内の「動線管理」と「ラインバランシング」がテーマです。
在庫の配置と動線管理で倉庫内作業の生産性と安全性の向上を図る
各企業の拠点として、多くの人やモノが集まる物流倉庫。自社の生産性の向上を図るうえで、倉庫内の環境や作業内容を適切に管理することは重要な要素の一つです。今回は、実際に作業者が動く「動線」の改善と、各工程の作業量を最適化する「ラインバランシング」の2つの手法について見ていきましょう。
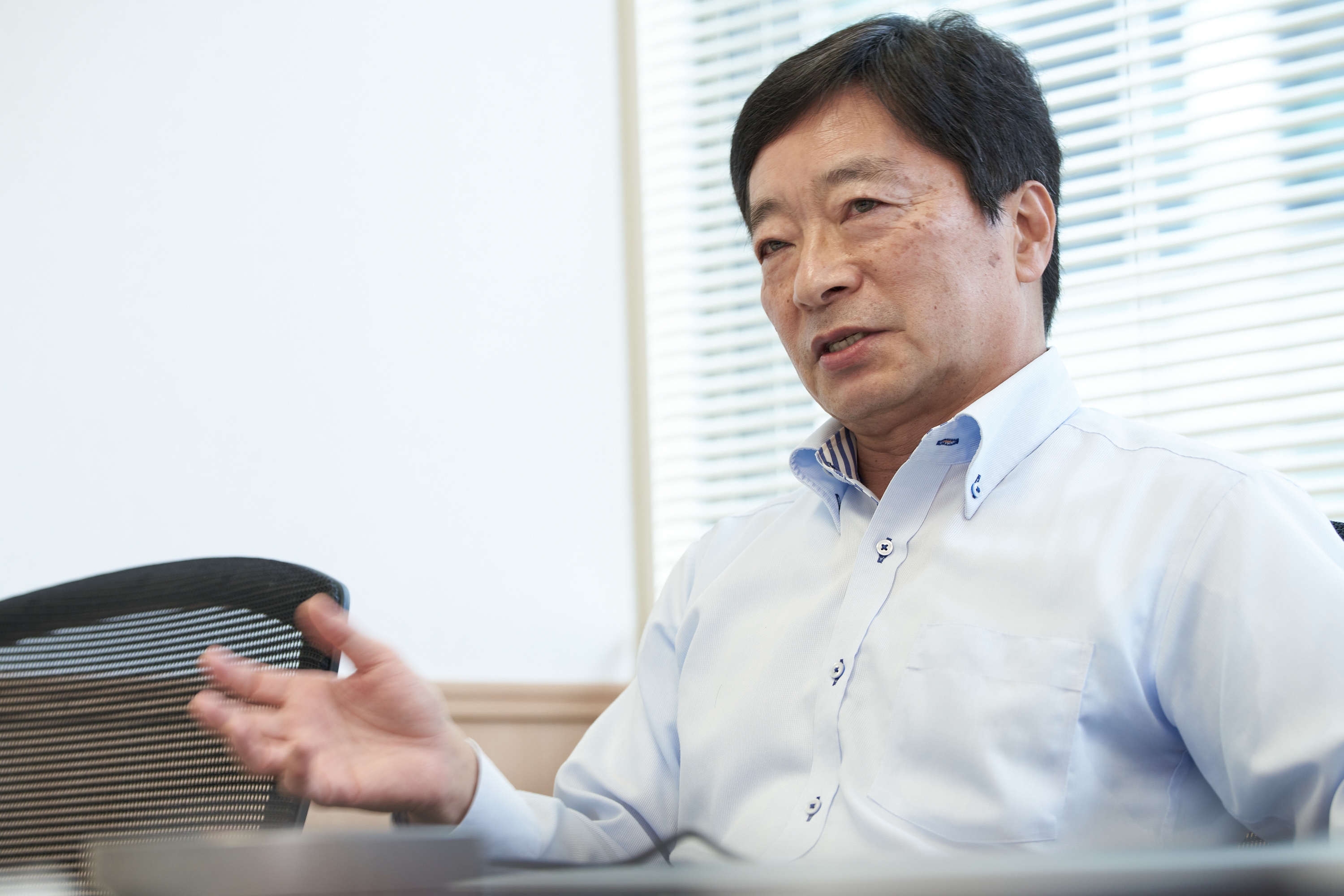
中小企業の物流倉庫では、在庫を品目ごとに置いているケースが多くあります。これは、作業者が直感的に把握しやすく、見た目がわかりやすいなど、一見使いやすく整理されている状態に見えます。しかし、実際に作業を見てみると、倉庫の奥へ置かれた在庫品を何度もピックアップしに行ったり、複数フロアを往復したりするなど、ムダな移動が発生しているケースも少なくありません。在庫の配置が実際の作業内容と連動していないのです。
そうした状況を改善するためのカギとなるのが、在庫品を出荷頻度(優先度)の違いで3つのグループに分け、特に重要なグループを重点的に管理する「ABC分析」です。
ABC分析の理論(2-8の法則)では、出荷頻度(または出荷量)の高い上位2割の在庫品を作業スペースや出庫スペースに近い位置にまとめて配置するだけで、倉庫内の動きの8割を集約できます。それに沿った適切な動線を設定することで、作業が効率化され、それまでピッキング時にかかっていたムダな移動時間も減少できます。ピッキング1件にかかる時間が短縮されれば、おのずと全体の作業量の向上も期待できるでしょう。また、安全性の面でも、移動距離が少なくなれば、その分事故のリスクも低くなるといえます。
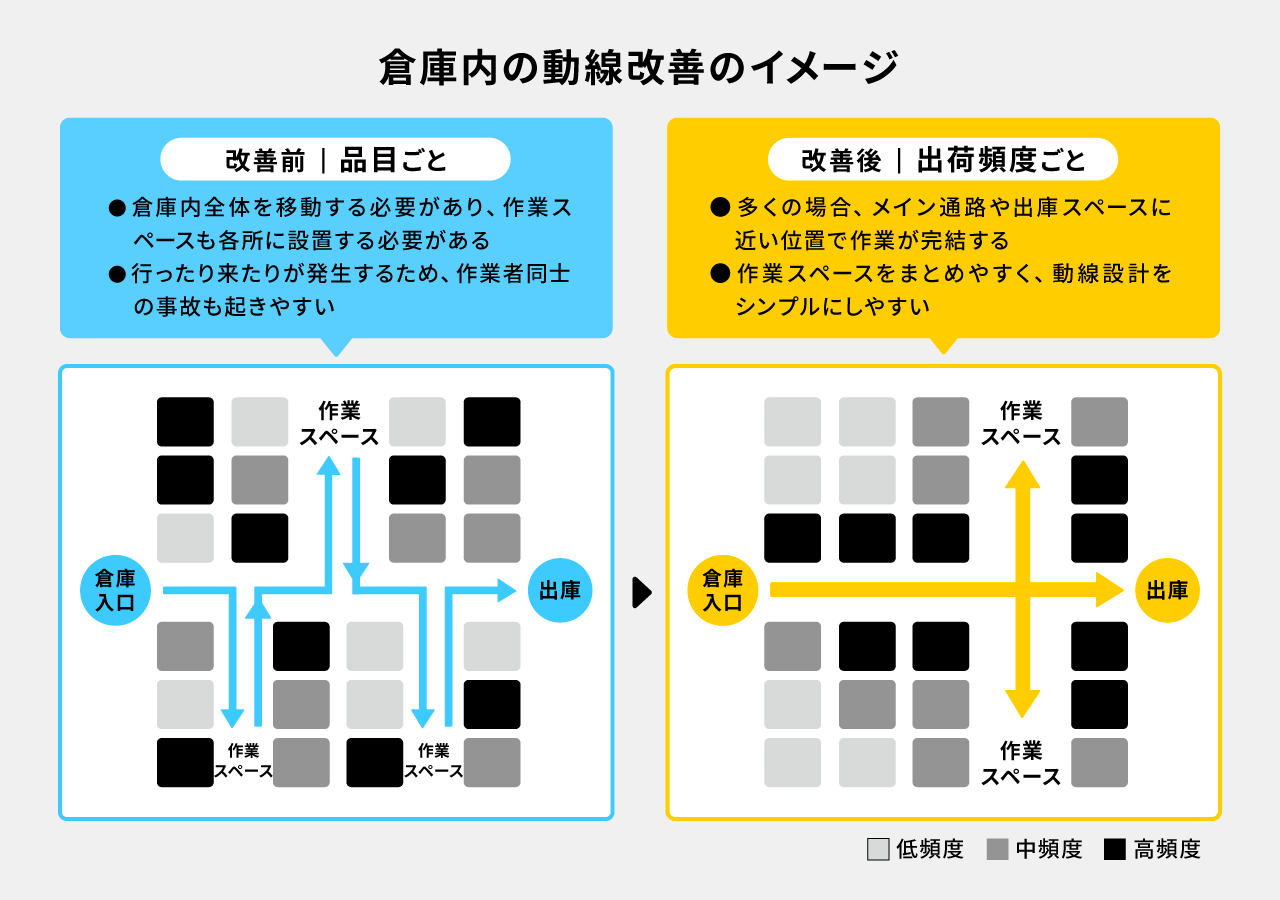
ABC分析の元となるのは適切な「数字(データ)」です。在庫品の出荷頻度(出荷量)はもちろん、一緒に出荷されることの多い組み合わせや、重量・大きさといった商品の情報まで、さまざまなデータを把握することで、倉庫内の在庫品の適切な配置と動線が見えてきます。
ABC分析についてはこちらの記事でも解説しています。
倉庫内の配置を整理することは、誤出荷や製品の破損を防ぐことにもつながります。
ある企業では、倉庫内がまったく整理されていなかったため物流工程での製品の破損や誤出荷の事故が多く、取引先の信頼を失ってしまったケースがありました。その企業は、製品の質はとても高く、海外生産も取り入れコストを抑えることで価格面での競争力にも強みを持っていました。それでも、倉庫内の事故の多発により、売上が落ち込んでいたのです。
その打開策として、同社は在庫のロケーション管理システムを導入し、倉庫内の在庫の配置や動線を見直すなど物流面での品質の改善を行いました。その結果、納品までの事故が減少し、お客さまの信頼も取り戻すことができました。
在庫のロケーション管理を行い、そこにABC分析を用いた最適な動線設計を取り入れていくことが倉庫内の環境を整える第一歩といえます。
ボトルネックを解消し、全体を最適化するラインバランシング
倉庫内での物流業務をはじめ、生産性のアップに欠かせないのが「ラインバランシング」の考え方です。ラインバランシングとはつまり、各作業工程における作業量のバラツキをなくし、「ボトルネック」を解消して全体を最適化する手法のことです。ボトルネックとは、全体の作業スピードを決める(限定する)要因となっていることを指します。例えば、引越し作業を思い浮かべてみるとわかりやすいでしょう。
高層マンションの最上階から家具を運び出す際、部屋から家具を運び出してエレベーターに乗せる人、下でエレベーターから家具を降ろし、トラックに積み込む作業者がいます。早く作業を終わらせようと上の階の作業者が一生懸命に家具を運び出しました。そうすると一見上の階での作業が捗っているように見えますが、エレベーターは決まったスピードでしか動かないため、エレベーターの前には家具がずらりと並ぶことになります。下の階で待機している作業者は、エレベーターのスピードに合わせて運び出していくため、上の階の作業スピードはまったく関係がなく、空き時間すら発生する可能性があります。
こうしたイメージは、物流倉庫の現場にも当てはめることができるでしょう。
倉庫内でピッキングから梱包、伝票貼り付け、出荷までの各工程が行われているとしましょう。そこにピッキングのスピードを大幅に上げるロボットを導入したとします。それによりピッキング工程の生産性(=単位時間あたりの作業量)は向上しますが、その後の梱包の工程などのスピードが従来通りであれば、全体で見た時の生産性アップにはつながりません。むしろツールの導入という投資が増えている分、生産性は下がったという見方もできます。
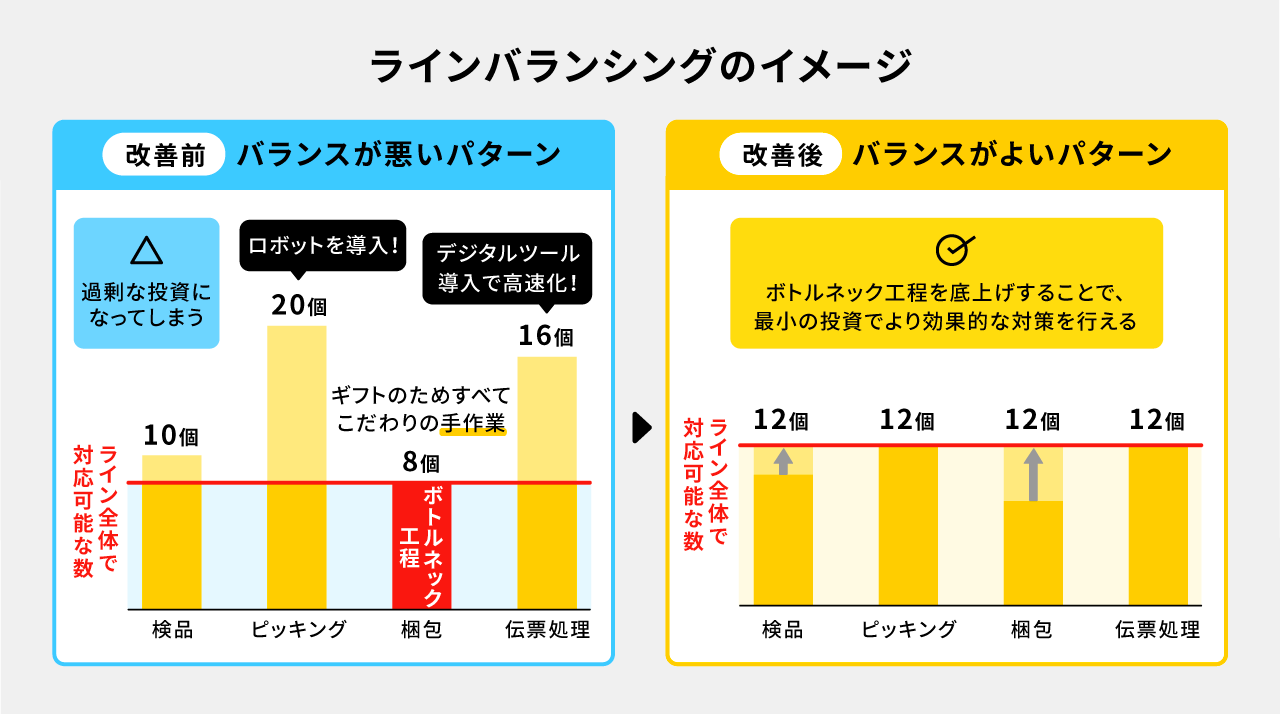
こうした状況を打破するためには、引越し作業におけるエレベーターのように、「全体のスピードを決定する要因」、つまりボトルネックに対して、適切に対処することが必要です。
物流倉庫において、工程間に潜むボトルネックを解消し、全体の生産性向上を目指すには2つの考え方があります。
1つは部門間を取り仕切る管理スタッフやシステムを組み込むことです。各工程の作業時間や効率性を把握・調整し、適切な人数や設備・資源の投入ができれば、コストを削減しながら、倉庫の持つ作業生産性を最大まで引き上げることができます。
もう1つは、一人の作業者が行える業務範囲を広げ、柔軟な人材移動を可能にすること、つまり「多能工化」です。極論ではありますが、一人の人間がすべての工程を担当していれば、無駄な待機時間は一切発生しません。もちろん属人化などの課題もありますが、ロボットによるオートメーション化など、多大なコストがかかる方法を除けば、究極のラインバランシングの実践ともいえるでしょう。
倉庫の課題に現場・経営の両面から向き合い、生産性が高く、働きやすい職場をつくる
物流倉庫内の「動線管理」と「ラインバランシング」の取り組みは現場側・経営側双方の気づきから始めなければなりません。現場目線では、作業のしにくさ、無駄な作業に対する地道な改善活動などを通じて、倉庫全体の生産性の抜本的な改善につなげていくことが重要です。こうした取り組みは、働きやすい環境づくりや効率化による労働時間の削減、現場での事故の減少など、作業者側にもメリットが大きいものです。
経営側から見ても、物流工程での事故や誤出荷の多発は会社への不信につながり、売上面での不振にもつながります。常に作業生産性や環境を管理する必要があるでしょう。
そこで重要になるのは、これまでのシリーズで扱ってきたように「データ」に基づいた判断です。
ロケーション管理やそれにもとづくABC分析はもちろん、各作業工程の作業量やボトルネックの把握など、感覚ではなく数字にもとづいて現状を把握し、合理的な判断を行なっていかなければなりません。そのためにも、自社の状況を手軽に確認できる管理システムをはじめとするDXツールの推進は、喫緊の課題ともいえます。
自社の作業生産性を高め、誰もが働きやすい企業体質をつくるためにも、まずはできる範囲から取り組みを進めていきましょう。
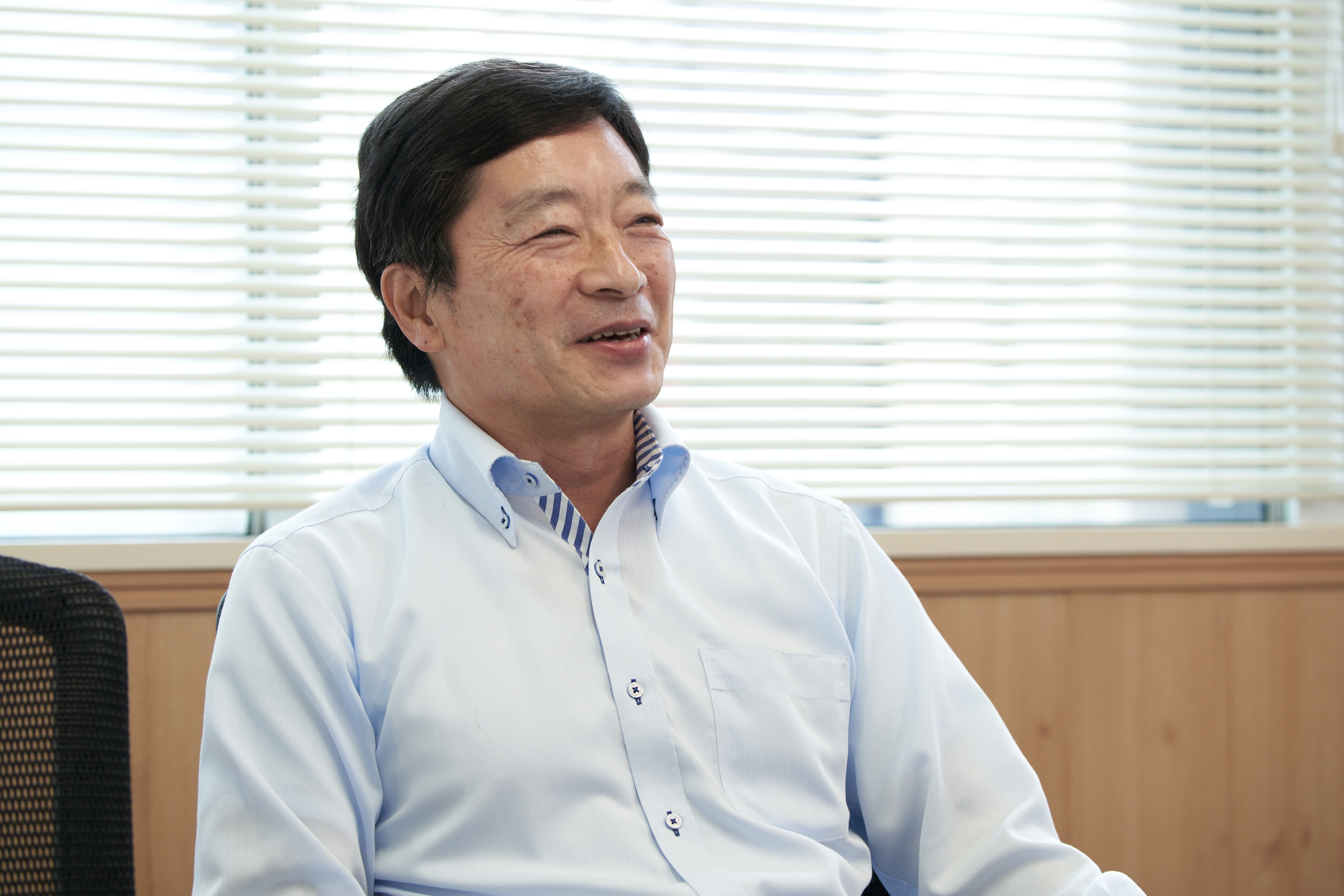