製造業の場合、製造現場の工場では生産性向上のためのさまざまな取り組み——例えば、「5S(整理・整頓・清掃・清潔・躾)」の徹底や生産ラインの最適化、「見える化」の推進、マニュアル・手順書の作成、——が積み重ねられてきました。しかし、その一方で、工場倉庫では同様の取り組みがあまり重視されない傾向にあります。工場倉庫における見える化・数値化や環境の整備といった身近な取り組みは、在庫の適正化や安全で確実な納品を実現し、事業の収益向上にもつながるものですが、まだまだ改善の余地が多く残されているのです。それだけに、製造業の工場倉庫の課題解決は取り組みがいのある課題だといえ、ぜひ前向きな意識を持って取り組んでいただきたいと思います。
「生産」「在庫」「納期」の3つの計画管理が倉庫整理の鍵
近年の製造業の事業トレンドを見ると、標準部品の普及やグローバル化の影響もあり、従来の系列に象徴される固定化された得意先のラインアップから、多数・多様な顧客・取引先を抱える水平型へと、事業の構造が大きく変化してきています。その中で、顧客別・出荷先別などきめ細かな在庫管理、納期管理、タイムリーなデリバリーが求められるようになってきました。これら高度化・複雑化するオペレーションを下支えするのが工場倉庫の役割であり、倉庫管理をしっかり行うことで、欠品・在庫切れ・納期遅れ・誤出荷などを可能な限り低減させていく必要があります。こうした在庫最適化の重要性については、「今、中小企業がデジタルとネットワークを駆使した在庫最適化を行うべき理由」でも解説しています。
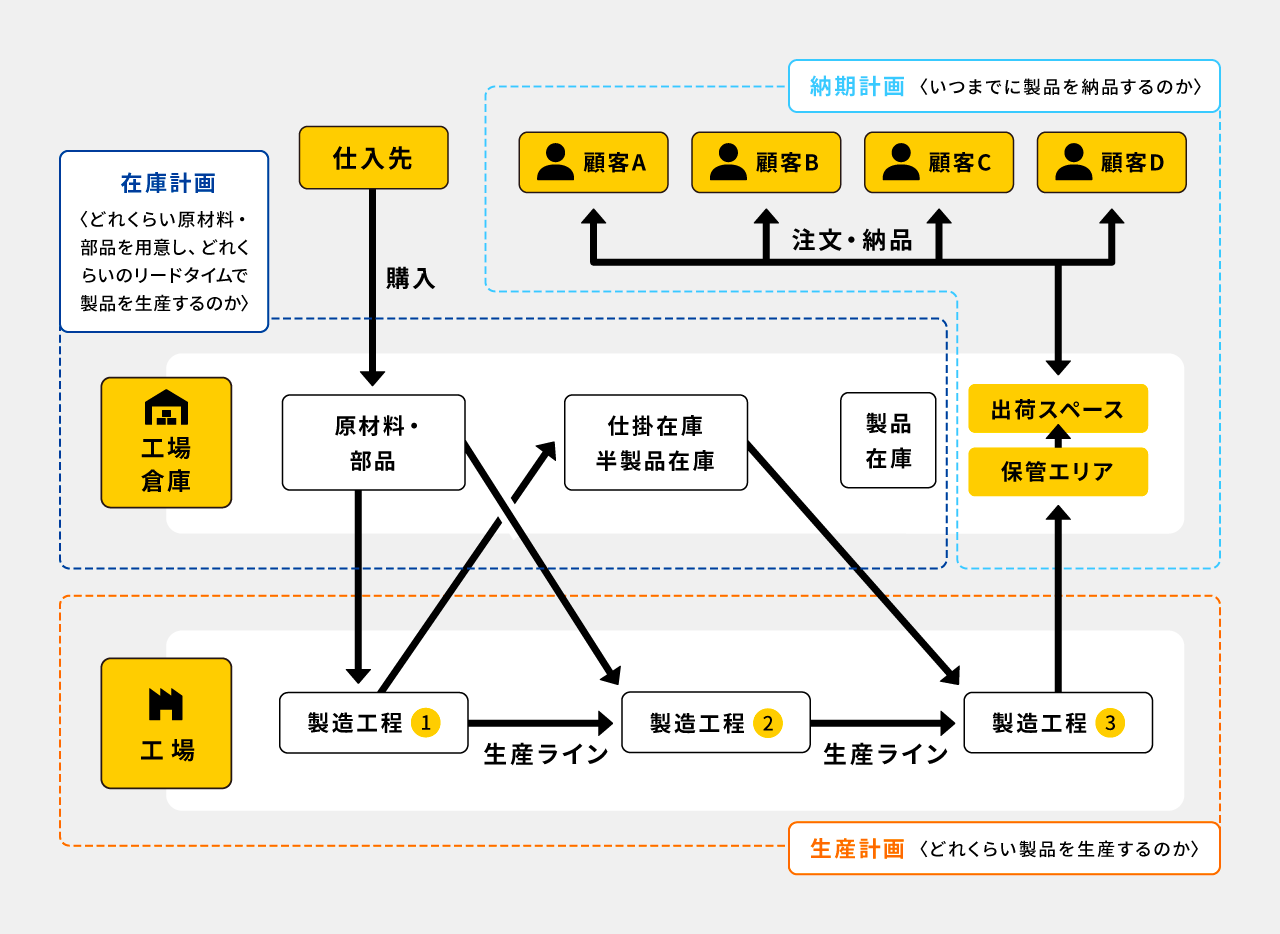
しかしながら、中小企業の工場倉庫の現状を見ると、課題が多くあります。
上の図に示したように、倉庫・在庫管理は、「生産計画」と「在庫計画」と「納期計画」という3つの計画に基づいて遂行される業務です。「どれくらい製品を生産するのか」という生産計画と「どれくらい原材料、部品を用意して、どれくらいのリードタイムで製品を生産するのか」という在庫計画、「いつまでに製品を納品するのか」という納期計画が噛み合っていない、すなわち、3つの計画がうまく同期していないことで、在庫が膨らんでしまうという問題を抱えている中小企業が多いのではないかと思います。
在庫管理の改善が進まない理由はいろいろあるでしょうが、最も大きな問題点として、「納期管理がしっかりできていない」ことが挙げられると思います。納品は、工場倉庫における重要なゴールです。納期から逆算して、「1日にこれぐらい生産できて、これぐらいの在庫が残っているから、このスケジュールで納品できる」という具体的なイメージを常に持っている状態が理想です。しかし、工場の生産ラインの進捗状況がきちんと把握できないために「納期に間に合わないと困るから、早めに、多めに生産しておこう」と考え、原材料や部品の在庫も、仕掛品在庫・半製品在庫も多めに持ってしまうのです。あるいは、「工場を稼働させていないのはムダ」とばかり、生産ラインを必要以上に稼働させれば製品在庫が膨らんでしまいます。
こうした3つの計画の関係を理解し、納期管理をしっかりと行うことが重要です。そのためには、個人の経験則や感覚に頼るのではなく、数値化・見える化を通じて、誰もがわかりやすい形での管理を実現することが必要になります。こうした課題解決が、必要な数量をタイムリーにデリバリーできる仕組みづくりにつながります。加えて、従業員に対し、「ムダがどうして発生するのか」「この在庫は本当に必要か」といった意識を徹底させることも重要です。
エクセルシートを活用した「納期管理」で課題解決
では、ここからは、どのように納期管理を行っていけばよいかを見ていきましょう。
製造業の中小企業における納期管理では、まずは扱いやすいエクセルシートを活用する方法が実戦的で、役に立ちます。実際に多くの中小企業がエクセルシートを使っていると思われますので、それに沿ったやり方を具体的に説明していきます。
納期管理に当たっては、まず現状の在庫(実在庫)を確認した上で、①どの製品を、いくつ、いつまでに生産するのかという「生産計画」を策定します。②これまでの「生産実績」があれば、それも記録します。
同時に、③作った製品をいつ出荷するのかという「出荷計画」と、④「出荷実績」も記録します。このとき、出荷計画は、「納期が○月○日→輸送に△日かかる→だから出荷は□月□日する」というように、納期日から逆算して決めていきます。
以上の項目を念頭にどれくらいの在庫が倉庫内に必要かを考えていきますが、納期と生産量、在庫量の関係をしっかりと把握するために、一覧表(テーブル)にまとめて整理しておく必要があります。
ここで力を発揮するのが、エクセルシートです。エクセルシートを使うことで自動計算ができますから、細かい数値の入れ替え、書き換え、更新の多い納期管理では、エクセルシートが非常に便利なのです。
ただし、注意点もあります。最も注意すべきなのは、以前の数値の入れ替えなどがきちんと行われておらず、誤った数値がシート上に残らないようにすることです。1人の作業者だけにエクセルの管理を任せてしまうのではなく、2人以上でチェックして、ミスを防ぐようにする必要があります。
また、複数の人がエクセルシートを独自に保存して別々に管理していると、どのファイルが最新のファイルなのか分からなくなるというリスクもあります。そこで、最近は、グーグルのスプレッドシートを使い、リアルタイムで書き換え情報なども共有するスタイルの採用が増えています。
納期管理の情報は、複数の部署をまたいで共有すべき情報です。その観点で、エクセルやスプレッドシートを活用したオンライン管理は、非常にメリットが大きいと思います。ただ、オンライン管理する場合、情報漏洩・流出などが発生しないよう、ファイル管理を各部署の責任者だけに限定するなど運用の社内ルールをつくっておく必要があるでしょう。
そして、エクセルシートを使った「納期管理シート」の運用がスムーズにいくようであれば、生産の進捗状況や納期などのスケジュールについても一覧できるように、「納期管理シート」を〝詳細化〟させることをお勧めしたいと思います。下図は、サプライヤー視点から詳細化された「納期管理シート」の一例です。
いつ・どれくらい生産する予定かという生産計画、実際にどれくらい生産したかという生産実績に加え、例えば、取引先の指定する納期、納期までのリードタイムを考慮した出荷予定、工場倉庫の実在庫と補充在庫の数量を、同一のシートに日付に沿って記入していきます。「納期管理シート」に、プロジェクト管理などに用いられるスケジュール表のような要素を加えることで、なお一層、見える化させることができ、極めて便利で有効です。
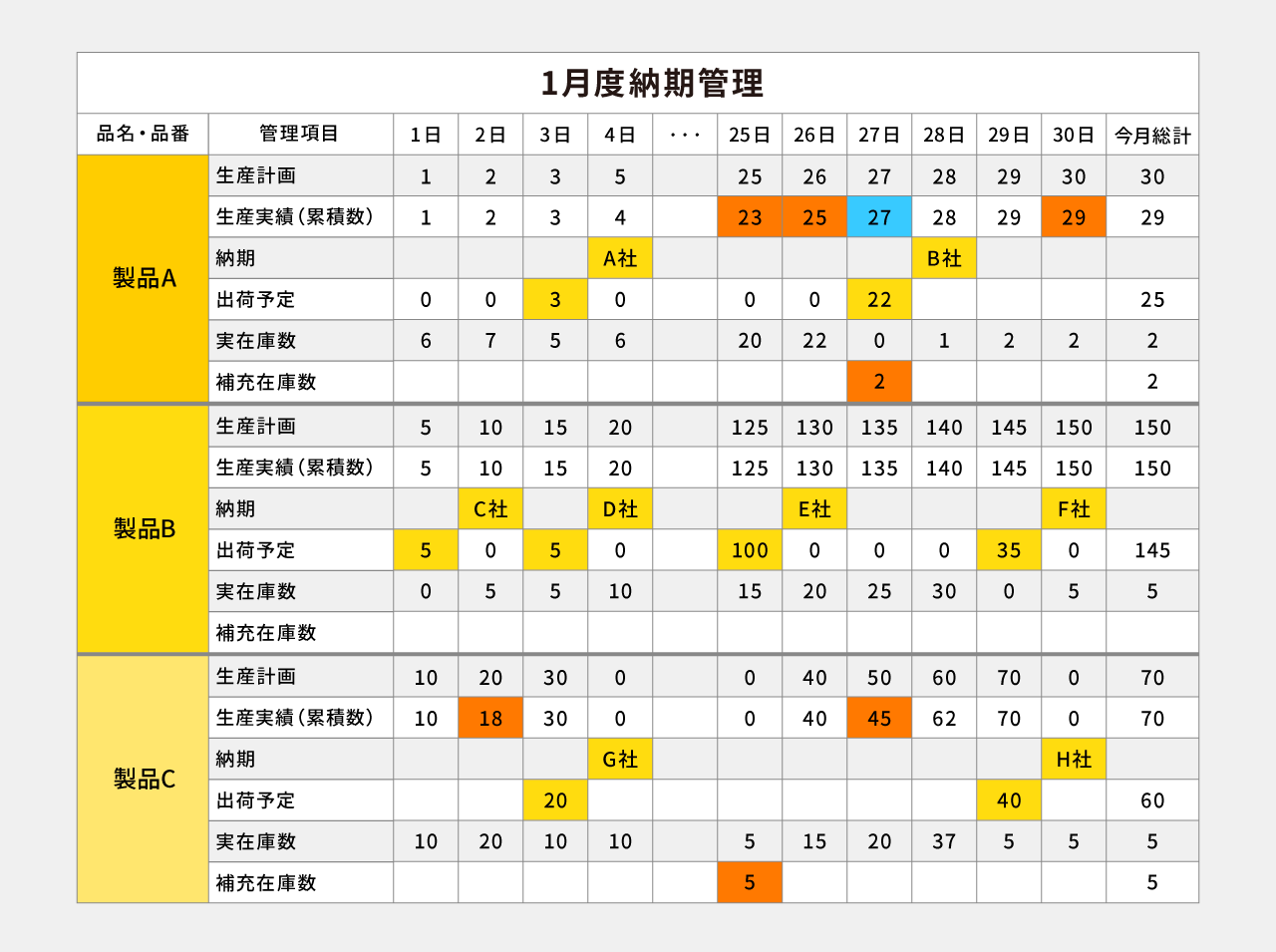
図2 サプライヤー視点での納期管理シート(月次)の一例
出荷のタイミングや数量をあらかじめ明記し、それに対する生産数や実在庫数、急な在庫補充数を日々記録していくことで、納品ミスを防ぎます。また、例えば「製品A」の25・26日のように、生産計画と実績にずれが生じた場合は、実際の在庫状況に合わせて、生産計画の改善を図る必要があります。
エクセルシートを使った納期管理は、デジタル化による在庫の適正化の第一歩といえます。シートでの管理に慣れたら、より専門的な機能を持ったサービスの導入を検討するのもよいでしょう。
出荷頻度別に在庫を管理して倉庫整理を進めましょう
「納期管理シート」は工場倉庫の管理業務に有効なツールですが、完璧なシートを作成することはあくまでも手段であって、目的は、シートの運用を通じて「必要な生産量・必要な在庫量・必要な出荷量」を把握し、過剰在庫・過小在庫等の工場倉庫に関わる課題を解決することです。
その真の目的に沿って、工場倉庫内のオペレーションで注意すべき点を挙げておきます。
《先入れ先出し法の徹底》
欠品や過剰在庫を防ぐためには、最低限の原則として「先入れ先出し法」を遵守する必要があります。「先に作ったものから出荷、納品していく」という簡単な原則ですが、整理・整頓が行き届いていない工場倉庫では、先に作られた製品が高積みされた段ボール箱の下段の方にあって取り出せず、いつまでも出荷されず古くなってしまうという事態が発生します。こうしたことが起きないよう、先入れ先出し法を念頭に置いた工場倉庫内のレイアウト設備と整理・整頓が求められます。
《循環棚卸の実施》
循環棚卸は、在庫の種類やロケーションごとに作業日を決めて在庫数を突き合わせていく方法です。工場のオペレーションを停めず少人数で行えるので、帳簿と実在庫にズレがないかを、細かくチェックすることができます。「欠品や在庫過多などが発生していないか」をチェックするには、定期的な棚卸しを行うことが大切です。工場倉庫全体の在庫を一挙にチェックする「一斉棚卸し」は、長期に工場の創業を止められるタイミングでしか実施できませんから、適時に「循環棚卸」を実施する方法が良いでしょう。
《ABC分析の在庫管理への応用》
納期の管理に「ABC分析」の手法を応用することも、倉庫整理には有効です。「ABC分析」とは、製品や部品などを、売上高や出荷点数・頻度、コストなどの指標をもとに分け、優先度順に「A品目」「B品目」「C品目」として重要なものから効率的に管理していく考え方です。ここでは、出荷品目をその頻度によってランク分けしていきましょう。
まず、高頻度出荷品目をA品目とし、優先的・重点的にA品目の納期管理を行います。出荷頻度が高くモノの動きも頻繁に発生するため、管理する品目数が少なくても、出荷作業全体の中で大きな割合を占めることになります。エクセルシートでの納期管理や、先入れ先出し法・循環棚卸の実施も優先して行うことで、倉庫整理もかなりの成果が得られるはずです。
そして、A品目の納期管理で取得したやり方を、中頻度出荷品目(B品目)、低頻度出荷品目(C品目)にも広げていきます。中・小頻度出荷品目については保管効率を重視し、さらに、まったく出荷実績のなくなる不動在庫(デッドストック、D品目)となるようならば、納期管理以前の問題として思い切って在庫処分を行い、工場倉庫内の保管スペースを確保するようにするのがよいでしょう。
冒頭でも申し上げたように、製造業における倉庫の問題は、これまであまり重視されてこなかった領域です。しかし、ここまでの解説でお分かりいただけたように、倉庫の課題解決は、企業の生産性向上に直結するのです。さらに、製造業に求められる高度化・複雑化するデリバリーの要請に応えられる体制をいち早く構築することができれば、それは、企業の大きなアドバンテージとなるはずです。
そうした大きなビジョンの下の、目先の第一歩として、納期管理、倉庫整理があるという点を認識していただきたいと思います。
監修:鈴木 邦成(すずき くにのり)※掲載記事の内容は監修当時のものです。
物流エコノミスト、日本大学教授(在庫・物流管理など担当)。博士(工学)(日本大学)。
早稲田大学大学院修士課程修了。日本ロジスティクスシステム学会理事、日本SCM協会専務理事、日本卸売学会理事、日本物流不動産学研究所アカデミックチェア。ユーピーアールの社外監査役も務める。専門は、物流・ロジスティクス工学。