【プロフィール】 ※掲載記事の内容は取材当時のものです。
鈴木 邦成(すずき くにのり)
物流エコノミスト、日本大学教授(在庫・物流管理など担当)。博士(工学)(日本大学)。
早稲田大学大学院修士課程修了。日本ロジスティクスシステム学会理事、日本SCM協会専務理事、日本卸売学会理事、日本物流不動産学研究所アカデミックチェア。ユーピーアールの社外監査役も務める。専門は、物流・ロジスティクス工学。
近年、中小企業の製造業の「日本のモノづくり」における重要性にこれまで以上の注目が集まっています。また、近年は部品などの標準化やモジュール化が進み、サプライヤー(原材料・部品メーカーなど)の取引先や顧客がこれまで以上に多様化し、その選択肢も可能性も大きく広がっています。
しかし、そうしたなかでも、サプライヤーは、ジャストインタイム方式などに代表されるタイトな納期設定に対応しつつ、適正在庫を維持していくことを求められています。
顧客企業が増える傾向にあれば、それぞれの顧客企業にあわせた在庫戦略や在庫レベルの設定も必要になってきます。
いかに在庫適正化を実現し、物流効率の向上を進めていくかということを考えていきます。
なお、本文中で在庫適正化のプロセスを実務の視点から理解しやすいように実際の数字とは若干、異なりますが、ケーススタディとしてボックスで紹介しています。
中小企業にとって在庫が適正であり続けることの価値は大きい
適正在庫量を設定して過剰在庫、過少在庫を解消する
近年、日本のモノづくりの中心として、部品メーカーの重要性にこれまで以上の注目が集まっています。標準化やモジュール化が進み、取引先が増えたり、ビジネスの選択肢も広がってきたりしています。質が高い日本製の部品が多方面から求められているといってもよいでしょう。
ただし、それゆえにこれまで以上にしっかりしたかたちで解決しなければならない課題も少なからず抱えることになります。
なかでも日本の部品産業を支える多くの中小企業の製造業を悩ませているのは在庫管理しょう。
「欠品が多くて、納品が大幅に遅れてしまった」「需要変動を見誤り、在庫が過剰になってしまった」「適正な在庫水準がわからない」「在庫過剰でスペース不足に陥っている」といった課題が出てくることも少なくありません。
在庫は多すぎても少なすぎても問題が生じると考えられています。すなわち適正在庫を設定し、それに基づいての在庫管理が重要になるわけです。適正在庫を基準とし、多すぎる在庫を「過剰在庫」、少なすぎる在庫を「過小在庫」と呼んでいます。(図1)
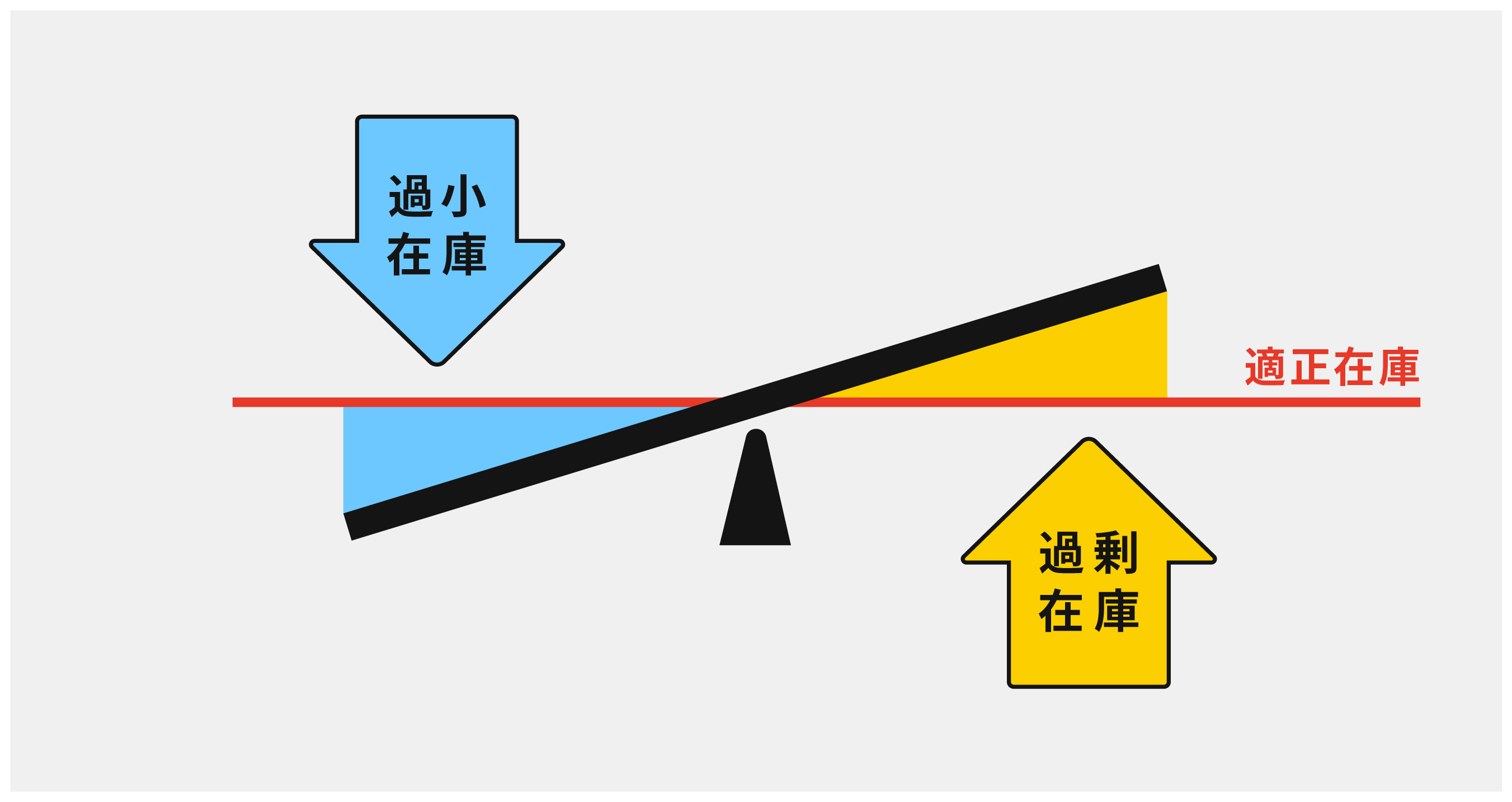
在庫とは会社の資金が利益になるのを待っている状態です。商品在庫は売れてはじめて売上げ、利益となります。在庫のままでは売上げも利益も伸びません。在庫はいくら長期にわたって大量に保有されていても、企業の利益に直結することはないのです。在庫のままでは「資金が寝ている状態」が続くことになります。したがって過剰在庫は、結局は売上高、利益の減少にもつながることになります。
ただし適度の在庫が存在しない「過小在庫」の状態も企業にとって好ましいとはいえません。「注文が多いのに在庫が十分でないためにビジネス機会を逃してしまう」というケースも少なくないでしょう。
実際、在庫戦略を綿密に練ることは容易なことではありません。多くの企業が悩まされています。
一見、容易なことにも思えますが実務となると相当な手間がかかることが多々あります。
なぜならば「企業全体のバランスを考えると必要のない在庫でも、各部署にとっては在庫を抱えるほうが業務を進めやすい」というケースも少なくないからです。
大量調達、大量生産、大量輸送、大量販売などをタテ割り組織のもとに行えば、大量の過剰在庫が生じる危険性があります。「在庫は放置すれば自然に増えていくもの」と考えて間違いないでしょう。たとえば調達・購買部は、大量に購入するほうが仕入れコストが安くなるから大量調達のほうが業務能率は上がるはずです。必要な商品を必要なだけ調達・購買するのでは仕入れでの大量値引きなども期待できません。
だがこうした大量調達、大量生産、大量在庫が場当たり的に行われれば、莫大な過剰在庫につながる危険も高いのです。
さらにいえば在庫適正化を実現するためには生産地から消費地までのモノの流れと在庫戦略とITによる一連の情報管理を巨視的、統括的、効率的に管理する必要性もあります。(図2)
改善前
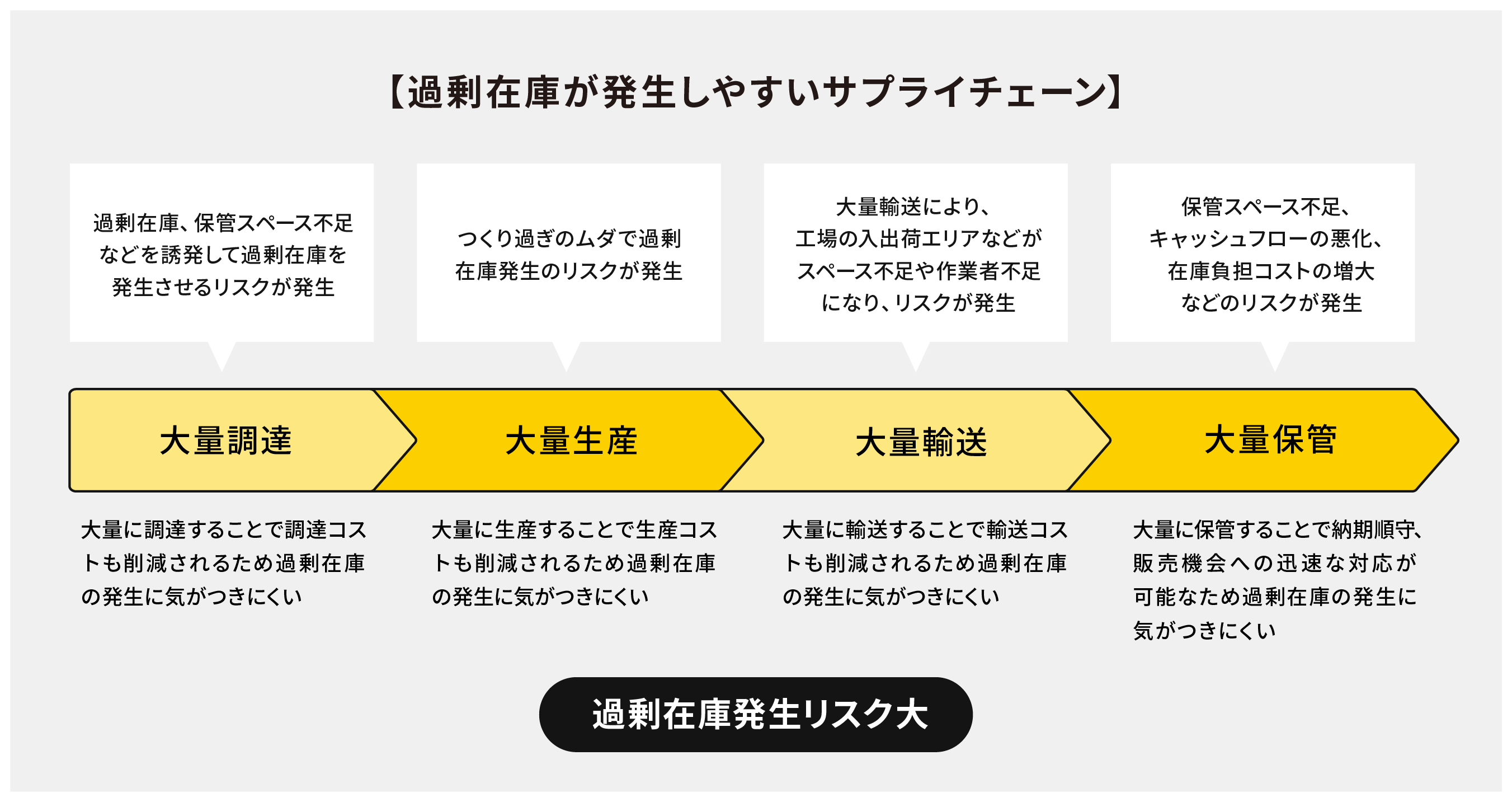
改善後
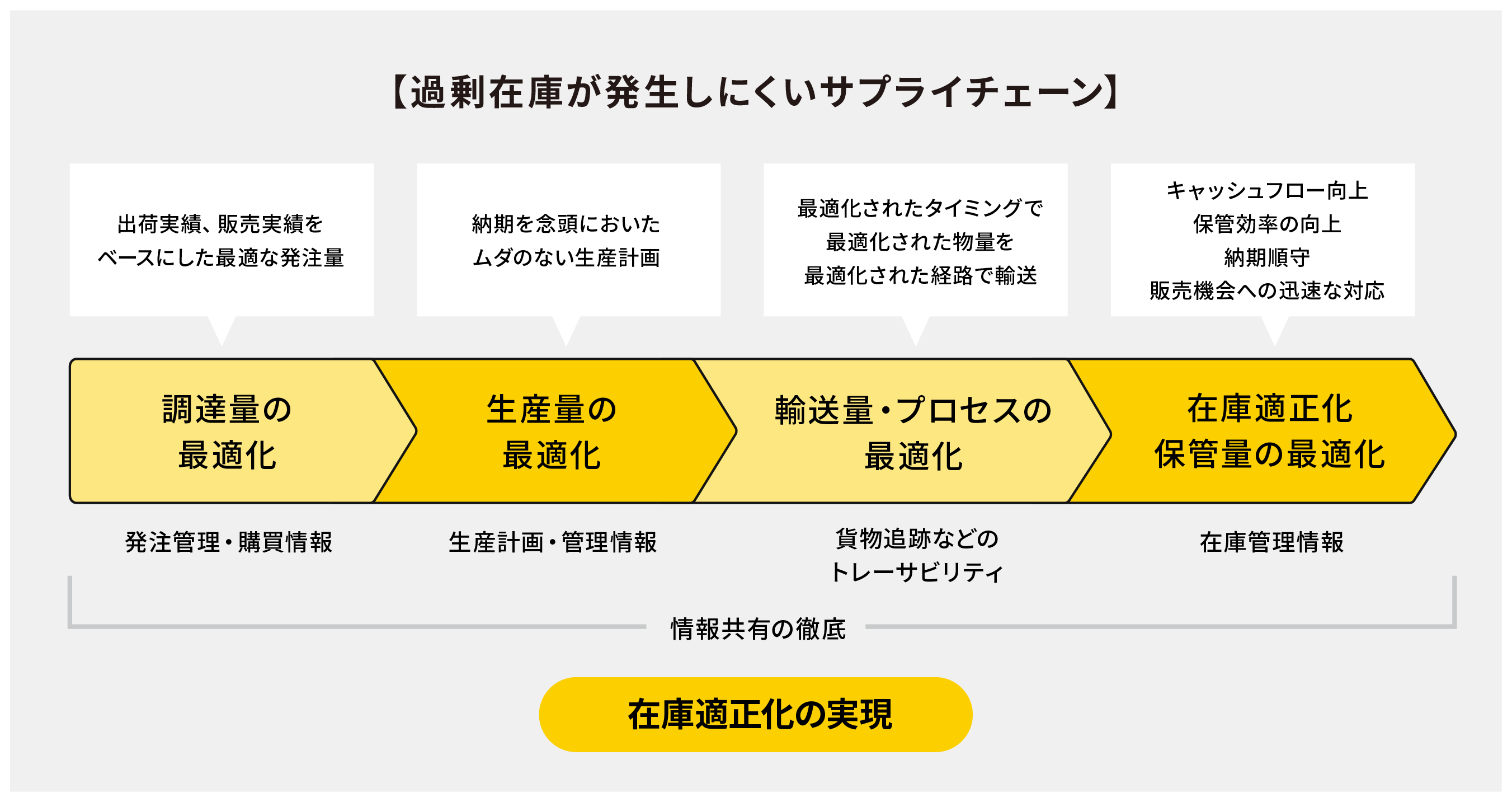
在庫が適正でないことが業務や経営に与える影響は?
在庫の基本的な機能がきちんと発揮され、そのデメリットが最小限に抑えられる在庫量を「適正在庫量」といいます。過剰在庫や過小在庫という状態を「異常だ」と迅速に察知するためにも正常な状態である適正在庫量を正確に把握することは重要です。
適正在庫量は需要予測、生産計画、販売目標、キャッシュフロー、在庫期間、リードタイムなどのさまざまな要因を考慮して決定されます。好景気ならばやや多めに設定する必要があるかもしれませんが、不景気ならば反対に少なめになるでしょう。
なお、適正在庫にある程度の幅があると考えた場合、その幅の下限を「安全在庫」といいます。品切れを避けるための最小限の適正在庫量を指します。ただし、一般に日本企業は欧米企業にくらべて適正在庫や安全在庫を多めに設定する傾向があるともいわれています。適正な在庫量をこれまで以上に徹底的に検証する必要もあります。
ちなみに部品関係の製造業が関わる調達物流や生産物流では原材料、部品、完成品の在庫管理に加えて、仕掛品(原材料に少しでも加工作業などが行われた状態)、半製品(製造途中の製品)の在庫も最適化する必要があります。
アセンブラーは緻密な生産計画のもとに最適量の原材料、部品を発注し、ムダのない生産プロセスのなかで仕掛品在庫や半製品についても適正在庫量を設定し、需要予測、販売計画、出荷計画などに基づき、完成品の在庫レベルを決めていくことになります。
他方、サプライヤーはアセンブラーの求める納期に遅れることなく、原材料や部品を納品する必要があります。「在庫過少で欠品が多く、納期を守れない」といったことは極力さけなければなりません。ただし、もちろん、納期遅れを恐れるあまり、過剰在庫が発生すれば、キャッシュフローが悪化してしまうリスクが出てきます。
ちなみにキャッシュフローと在庫管理は密接な関係にあります。
キャッシュフローとモノの流れは正反対になります。製品が滞ることなく出荷されて在庫が減れば、キャッシュフローは増えます。反対に在庫が増加すれば、キャッシュフローは減少することになります。つまり在庫に注目していれば、キャッシュフローがどのような状態になっているかが簡単にわかるのです。もちろん、キャッシュフローが健全ならば余裕のある資金繰りも可能となります。
在庫が削減されれば、キャッシュフローは大きくなるというわけですが、手がつけられないほどの過剰在庫ともなれば、経営が大きく圧迫されることにもなりかねないのです。
調達物流:原材料、部品などをサプライヤー(部品メーカーなど)からアセンブラー(組立ラインを持つ製造業)が調達する物流領域
生産物流:工場内での入出荷管理、在庫管理、包装・梱包作業などの一連の物流工程
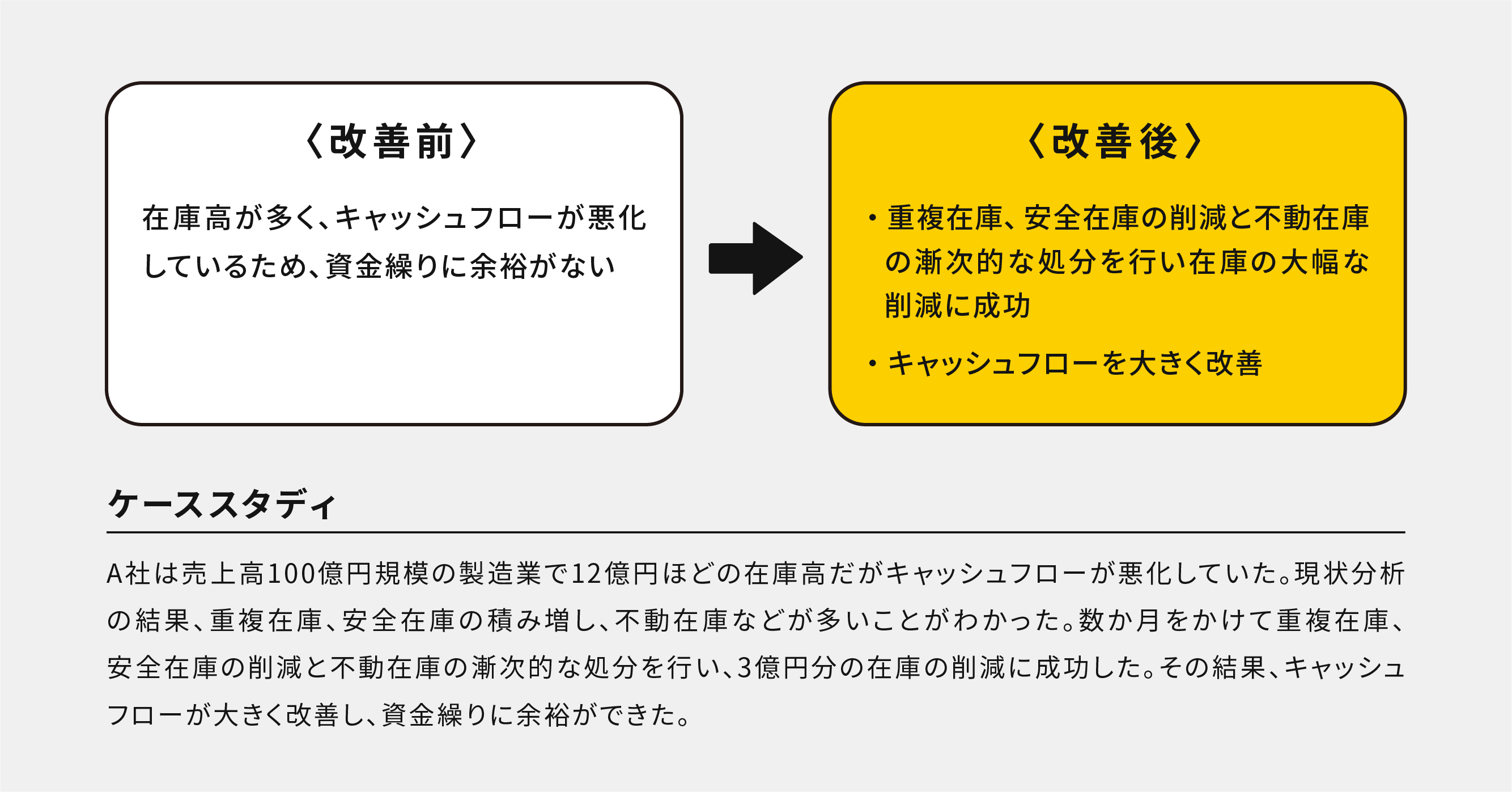
在庫の適正化ができていない原因は?
一般的に企業活動を活発に行うと在庫は自然と増えることになります。「適正在庫量を維持していくことがなかなかできない」という悩みを抱える企業は少なくありません。
製造業の在庫管理を考える場合、アセンブラーの視点から考えると、「必要なときに、必要なモノを必要なだけ、供給すれば在庫過剰に陥ることはない」ということになります。すなわち「ジャストインタイム方式」での在庫管理が理想となるわけです。
けれども、サプライヤーの視点から考えると、事情は逆転します。
「アセンブラーの求める納期に応じられるように欠品などのないように対応しなければならない」と考えることになるからです。その結果、アセンブラーに迷惑をかけないように安全在庫を多めに設定して、多めに在庫を持つことで納期を順守しようとする傾向が強くなります。実際、過少在庫となり欠品が発生しやすくなる在庫状況に陥れば、取引先の信用を瞬く間に失ってしまうかもしれません。
安全在庫が必要以上に増えてしまい、景気動向が変わったり、需要変動の大きな波に直面したりすれば、たちまち安全在庫と考えていた在庫が、過剰在庫に変わってしまうのです。したがって、在庫適正化の実現にあたっては需要予測や生産計画や在庫情報の共有は絶対に必要になります。
在庫拠点が複数ある場合などは拠点ごとに在庫を持つため、安全在庫が積み増しされ、過剰在庫の要因となることもあります。また入出荷業務が標準化されていない手作業中心のために在庫精度が低くなっていることもあります。
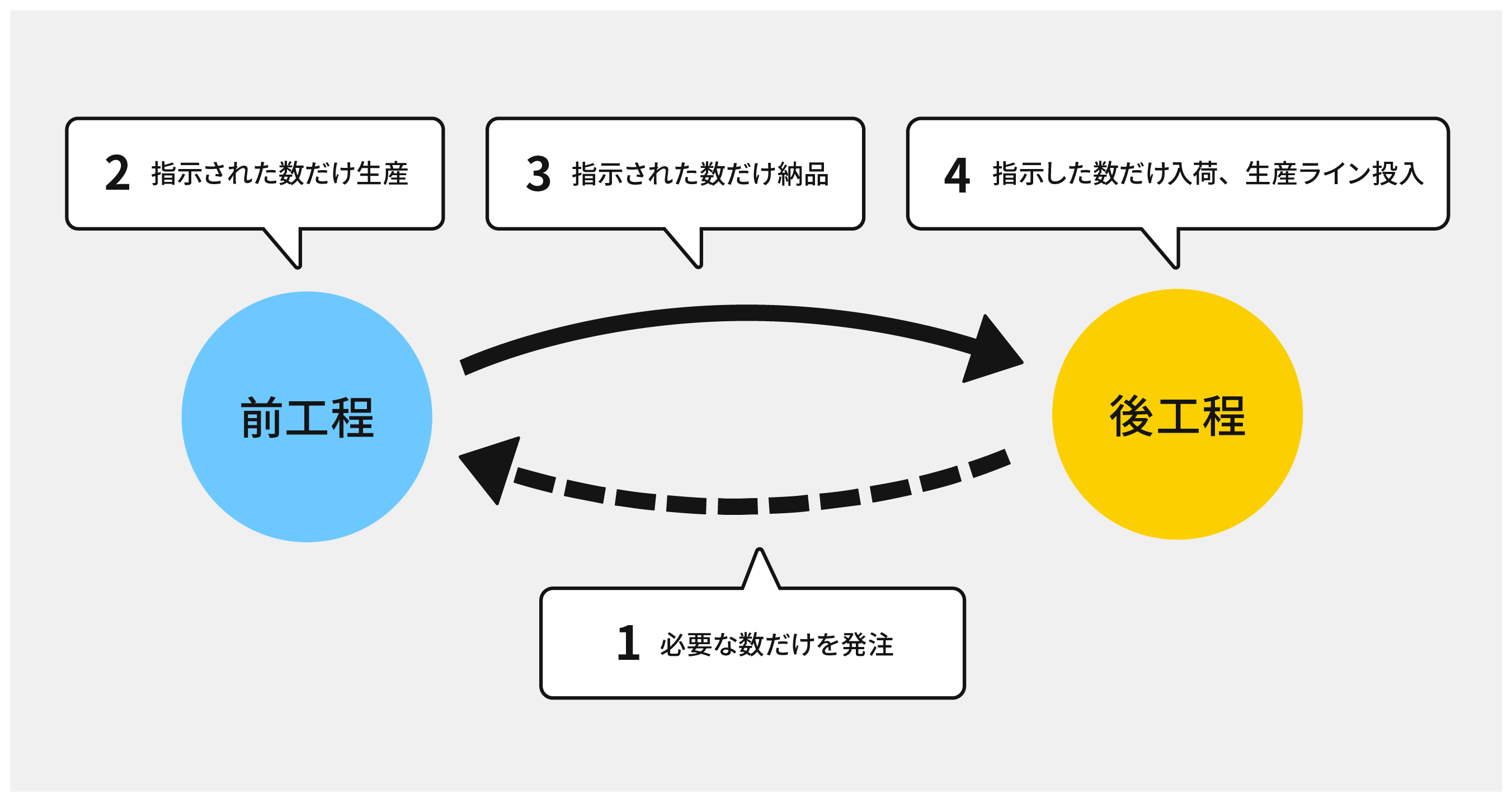
JIT(ジャストインタイム):自動車業界で導入されている「必要なときに必要なモノをムダ、ムラ、ムリなく供給する」という方式。在庫最小化を図るうえで大きな効果を発揮する。ただし、導入にあたっては多大なノウハウが必要とされる。
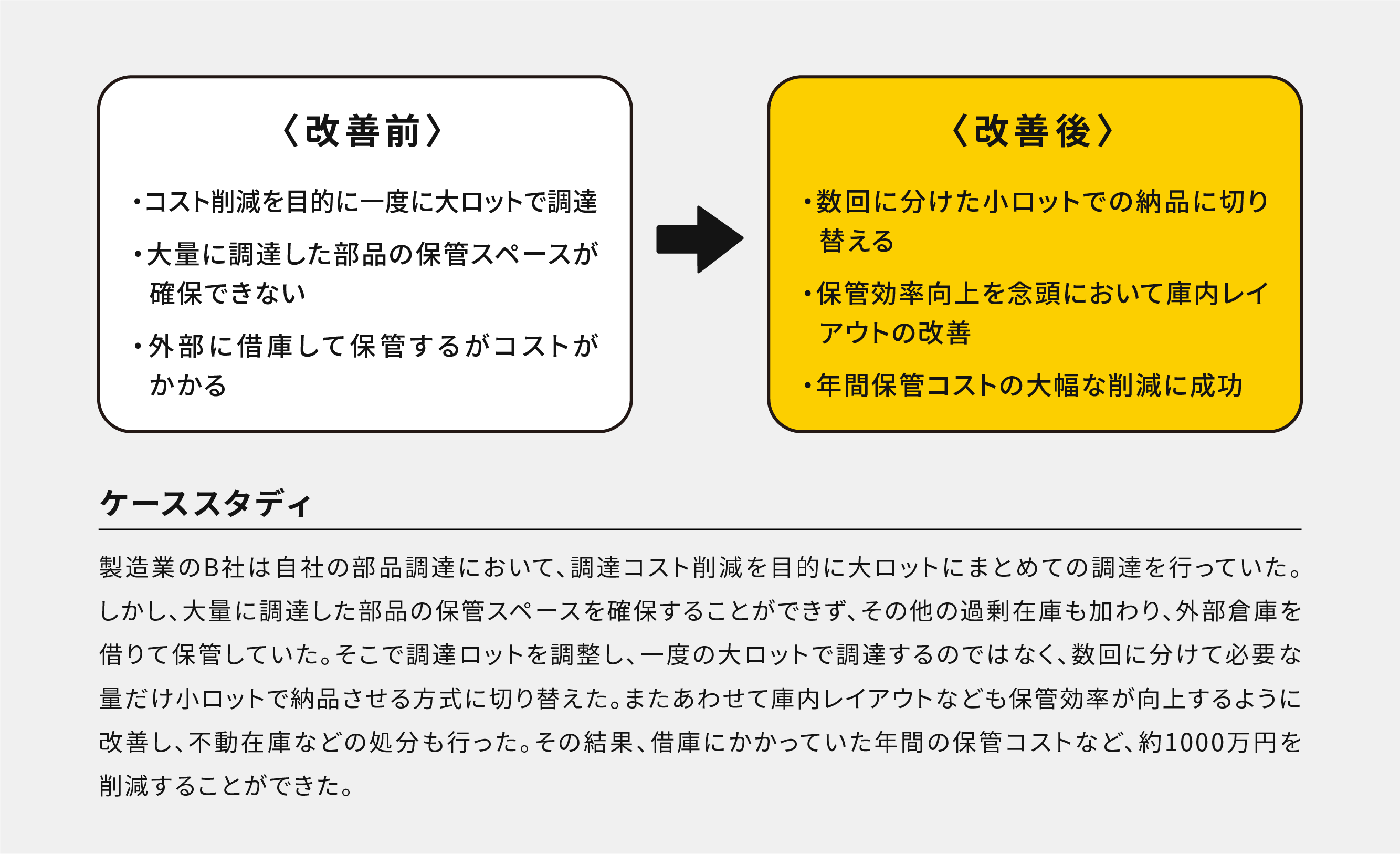
在庫が適正化されることで期待できるメリットは?
現代経営では「在庫は悪」という考え方が主流となってきましたが、実は製造業が在庫を持つことにはそれなりのメリットがあります。
在庫を少ししか持たない生産工程ではピーク時に大量生産をしたり、作業者を確保したりしなければなりません。しかし在庫を多めに保有することで工場の操業時間などの平準化を実現できるのです。また、納期の前倒し変更や追加受注、飛び込みの注文などにも柔軟に対応することができます。工場のラインも販売状況の上振れに左右されることなく稼働さえることができますし、納品ロットや荷姿も平準化が可能です。
けれどもそれでも過剰在庫を避けて、適正在庫量を維持しておきたいのは、過剰在庫のデメリットを無視できないからです。
製造業の場合、過剰在庫の陰に生産ラインの問題が隠れていることもあります。たとえば、生産設備の調子が悪くても、在庫が必要以上にあれば、生産性のムダが発見されないかもしれません。またつくり過ぎの環境なのでどれくらいの人員過剰が発生しているかをなかなか掌握することができません。
在庫を適正化することでそうした現場のムダや矛盾も明らかになってきます。
また工程間に仕掛品がある場合、製品化されるまでの時間がどうしても長くなりますが、仕掛品在庫を減らして作業するようにすれば必然的に生産リードタイムを短縮することも可能になりますし、製品間の品質のバラつきも小さくなります。
もちろん、過剰在庫の山のなかで作業したり、欠品がしょっちゅう発生したりするような現場ではなく、最適化された在庫環境で働くことで従業員のやる気も高まることになるわけです。
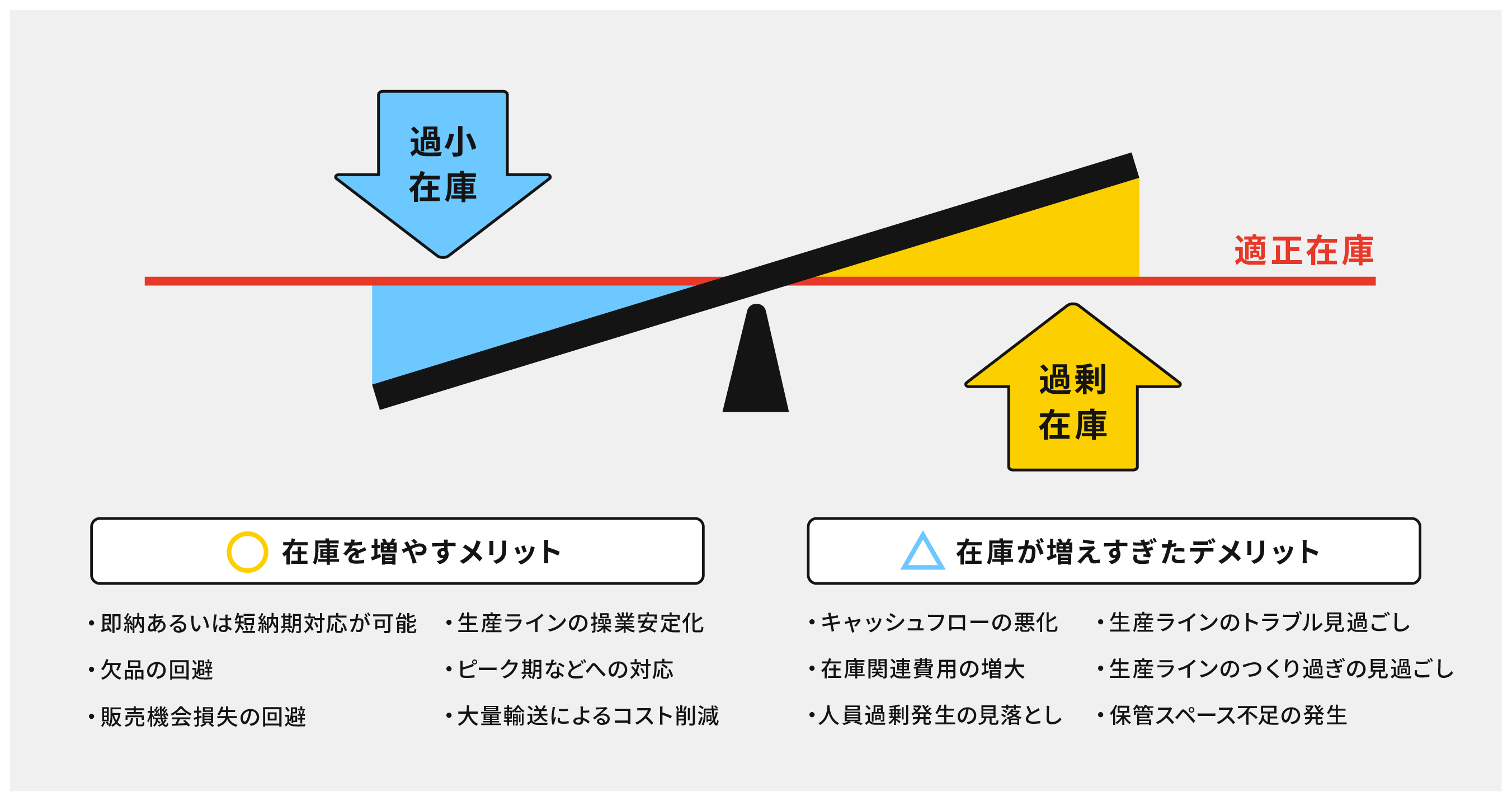
在庫関連費用にはどのようなものがある?その負担が経営にどれだけ影響を与えている?適正化でどれだけ改善される?
在庫が増えればそれにあわせて関連の費用もかかります。
こうした在庫のかかる費用を在庫費用、あるいは在庫負担コストなどといいます。その基本的な考え方について説明しておきましょう。
会計学上の在庫は資産となりますが、在庫が少なければキャッシュフローがよくなり、借入金なども少なくて済むわけです。
しかし在庫が増えればそれに応じて金利負担が重くなってきます。製造業の工場の現場の話でいえば、「つくり過ぎが原因で保管スペースが不足している」という状況です。外部倉庫などを借りれば追加的な保管費もかかることになります。またラック(棚)やパレット、段ボール箱、台車などを買い増しする必要も出てきます。自社で倉庫設備を増強すれば減価償却費の負担も大きくなります。
もちろん、在庫期間が長くなれば型落ちして商品価値が低下し、評価損となるリスクもあります。キャンセルや返品に応じる必要も出てきます。パソコン部品のようにプロダクトサイクルが短い場合、型落ちも早く、そのための在庫処分も行うとなればコスト負担も大きくなります。つくり過ぎということであれば直接工も増やしているでしょうからそのための人件費も増えているはずです。 また在庫保有にかかる「在庫金利」という考え方もあります。在庫金利といっても実際に金利を払うわけではありませんが、在庫に金利がかかるというコスト意識を植え付けるための指標として用いられます。確かに一般に在庫を抱えれば販売機会も増えるので売上高が増えるケースもあります。けれども在庫を多く抱えて売上高を伸ばしても在庫金利もその分増えるわけですから、必ずしも相応の利益を確保しているとはいえないのです。
そこで在庫最適化を達成するためには、製造業でいえばつくり過ぎとなっている在庫や欠品状態の在庫を適正レベルに調整する必要があります。
また最適在庫量にある程度の幅を持たせて、下限や上限を設定するという考え方もあります。下限とは必要最小限の在庫量、上限とは安全在庫を多めに設定した場合の比較的余裕のある在庫量です。
たとえば、安全在庫を多めに設定しているならば、これをある程度、落としても、「納期順守が可能か」「欠品が発生することはないか」といったことを検討することで、実務的な視点からの適正在庫量を導き出していくことも可能でしょう。
もちろんその結果、在庫を削減できることになれば、在庫費用や在庫金利もそれに応じて削減することも可能になります。
後編に向けて
ここまで、在庫適正化を目指すうえでの基本的な考え方を紹介してきましたが、後編では在庫最適化を実現するためにはどのようなイメージで進めていけばよいかを考えてみましょう。
製造業の在庫最適化を実現するためにはアセンブラーとサプライヤーの情報共有を徹底させる必要があります。生産計画や在庫情報の共有のもとに、欠品が発生しないように納期を順守していくなかで適正在庫を維持していきます。
そのための現状分析の方法や中小企業における在庫最適化の理想形などについて解説していきます。