
株式会社ドーム サプライチェーン本部 副本部長 石井宏史さん(左)
株式会社ドームユナイテッド ドームいわきベース センター長 澁谷晋司さん(右)
1996年にスポーツ用のテーピングの輸入販売会社として設立された株式会社ドーム。1998年より、アメリカのスポーツアパレル「アンダーアーマー」の日本総代理店になっています。2011年の東日本大震災で福島県いわき市に支援物資を届けたのをきっかけに、雇用創出を通じた復興支援を行うために物流センターを設立することにしました。そして2016年に完成したのが「ドームいわきベース」です。「魂の息吹く物流センター」をコンセプトに、自社グループによって運営しています。 ※掲載記事の内容は取材当時のものです。
株式会社ドームユナイテッド ドームいわきベース センター長 澁谷晋司さん(右)
1996年にスポーツ用のテーピングの輸入販売会社として設立された株式会社ドーム。1998年より、アメリカのスポーツアパレル「アンダーアーマー」の日本総代理店になっています。2011年の東日本大震災で福島県いわき市に支援物資を届けたのをきっかけに、雇用創出を通じた復興支援を行うために物流センターを設立することにしました。そして2016年に完成したのが「ドームいわきベース」です。「魂の息吹く物流センター」をコンセプトに、自社グループによって運営しています。 ※掲載記事の内容は取材当時のものです。

世界一の物流センターを目指すドームのドームいわきベースとは?
ドームの物流拠点は福島県いわき市にあるドームいわきベース(以下、DIB)。「魂の息吹く物流センター」をコンセプトにしたこの物流センターは、雇用を通じて震災復興の一助となりたいという思いを掲げ、2015年末に竣工されました。総面積16,315坪、天井高11m、搬送コンベヤ全長4.5kmという巨大な倉庫では、10代、20代を中心とした若い社員たちが活躍しています。目指すのは単なる復興だけでなく、ゼロからプラスに動かすための成長。スポーツを通じて人、モノ、お金が循環し、付随する環境が向上するという、欧米の地方創生モデルを参考に立ち上げました。

効率化のための具体的な施策について、現場責任者の澁谷さんが意識しているのは「優先順位のコントロール」だそうです。
「集品から加工、検品へのコンベアによる搬送で、なるべく止まらないように、かつ一気に流れて詰まらないように平準化を意識した優先順位のコントロールをしています。そのため、工程間のやり取りでも“何を”、“どれだけ”、“いつからいつまで”という情報を明示していますね」(澁谷さん)



大量の商品を正確かつ効率的に処理するノウハウ① 業務フローを意識したレイアウト
もちろん、DIBの物流施策が最初からうまくいった訳ではありません。現場がスムーズに運用できる環境を構築するために、数々の試行錯誤を行ってきました。「実は、当初はオペレーションの考え方に経営と現場のギャップがあり、現場に混乱が生じてしまっていました。店舗では、お客様から『閉店するんですか?』と聞かれたくらい商品を出すことができず、大混乱だったんです」と石井さんはいいます。
「設立当初は、『人ではなくモノを動かす』というセンターコントロールの考え方を軸に業務を進めていました。例えば、当初は個々のIDでログインすると優先順位の高い案件が表示され、人が判断せずともやるべきことが分かる状態にしていたんです。しかし、このオペレーションは、計画通りに全て実行されたときを前提としたもので、変更・変化には弱く、DIBのスタッフがこれまで行っていた方法とは合致しない部分も出てしまい、現場に混乱が生まれてしまったのです。そこで、現場の意見を聞きながらトライ&エラーを繰り返し、元々取り組んでいたラベルを使った情報の見える化と人が柔軟に判断するオペレーションへと切り替えました」(澁谷さん)


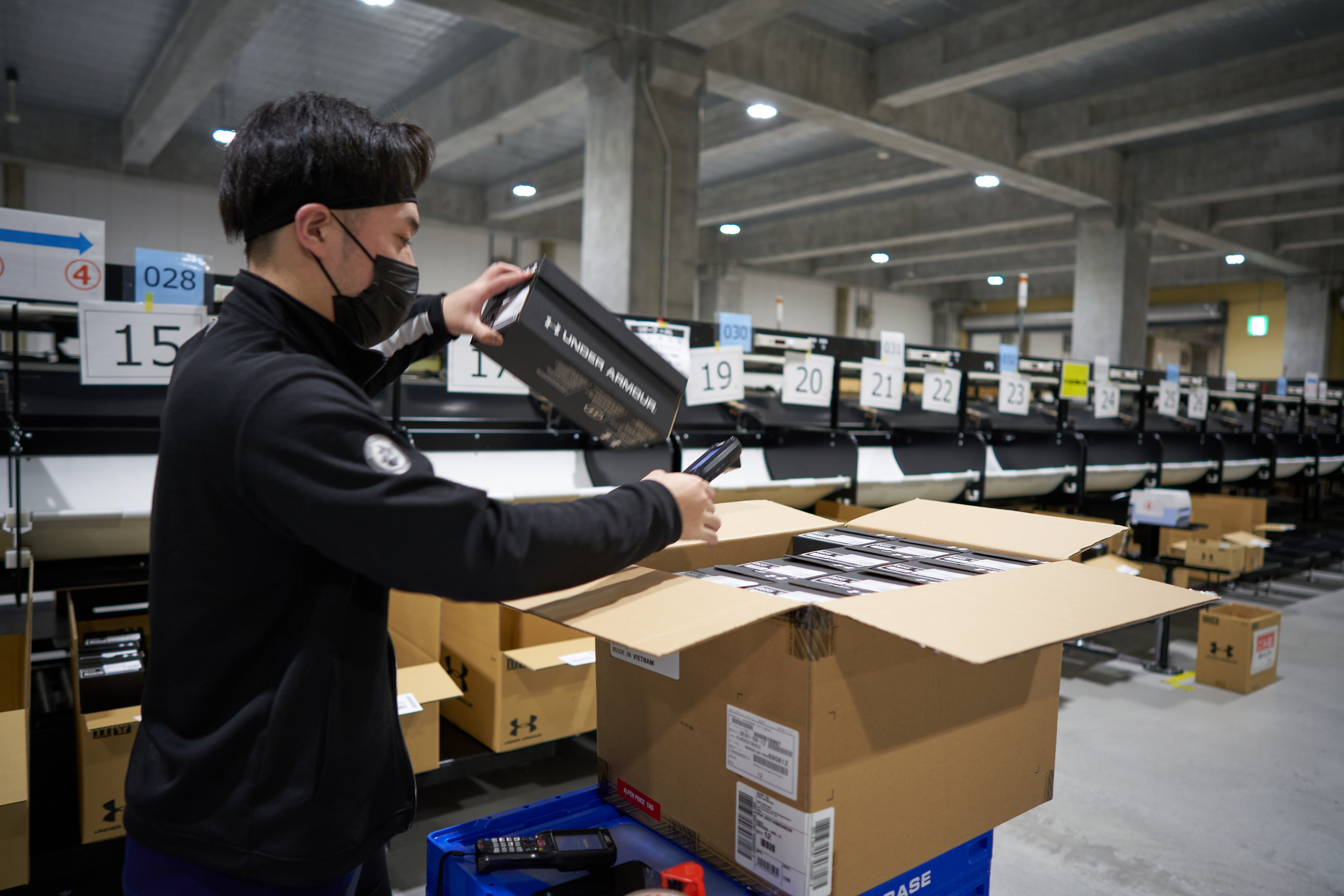
大量の商品を正確かつ効率的に処理するノウハウ②複数チャネルへの振り分け
DIBには、ほぼ毎日のように大量の商品が到着します。これらを一括で扱うのではなく、「いつ・どこに・何をどれだけ出すのかという出荷を想定することが大切。入庫計画、販売計画を事前に倉庫側に連携します。シーズンがスタートすれば、これまでの実績も見ながら、逆算して各オペレーションを考えることで業務の効率化を図っています。」と石井さん。大きくアパレル、フットウェア、先行値付け分と再生品で保管場所を分け、ロット数が多く頻度の少ないものは一等地を避けて保管。入出荷の実績に応じて配置転換し、出荷頻度の高いものを方面別に効率的に配置しています。
さらに、倉庫での処理能力をアップさせるためにおこなっている、現場の工夫について澁谷さんは次のように語ります。


大量の商品を正確かつ効率的に処理するノウハウ③作業計画の策定
物流業務は作業計画が必要不可欠です。石井さんも、「リードタイムの短縮にしても、スループットの最大化にしても、事前準備が重要です」と話します。
DIBでは粒度の細かなKPI指標を取りつつ、予実管理にて月単位で振り返りを実施。良かった点と悪かった点を評価して、今後の業務効率化に生かしています。ただし、「日ベースでの予定出荷数量の変動は避けられないため、営業との連携も重要になる」と澁谷さんはいいます。
「営業から日ごとの出荷予定数量のデータが共有されるのですが、時折数万ピース単位での差がでてしまうことがあります。物流側としては人員のコントロールにも関わってくる部分ですので、できる限りギャップが発生しないよう、営業と密にコミュニケーションをとりさらなる効率化を目指しています。また、毎日朝会にて前日作業を振り返り、当日作業の計画を確認することで、工程をまたいだ人員の配置や応援体制を構築。昼礼では進捗状況を確認し、必要があれば迅速に修正して遅れが出ないようにコントロールしています」(澁谷さん)

「みんながハッピーな状態でいられるよう、どこかに負荷が集中しなうようにしています。作業人員はデジタルで管理し、これまでの実績をすべてデータベース化して作業計画に役立てているんです」(澁谷さん)
入荷処理やラベル発行など、各作業にどれだけのMHを使ったか詳細に記録し、生産性の状況を細やかに分析。月にどのくらいのMHが必要かを工程別に算出することで、翌月以降の人員の配置を予測・計画しているのだそう。
「かつては計画と実際の誤差が大きく生産性が悪くなることもありましたが、最近はデータがたまったことで数値が改善されていますね。ただ、それでもイレギュラーな事態は起きるものなので、現場で判断したり、必要に応じで本社に問い合わせたりして対処しています。そうしたイレギュラーな事態も、対応後は記録に残し、『こうしたほうがいい』という意見を取りまとめて次に備えるようにしています」(澁谷さん)
通常は、倉庫は依頼されたものを入庫処理し、依頼された通りに出荷することが主な役割です。しかし、ドームでは倉庫からも各方面とコミュニケーションをとることで全社的な業務効率化を図っています。
「例えば、倉庫から営業側に『こうしたら効率的になる』『オペレーションをこうしてみては?』と改善案を投げかけているんです。
わたしたちが『魂息吹く倉庫』と呼ぶドームいわきベースは、震災復興や事業成長に加え、スポーツマインドを持った者たちが切磋琢磨しながら、『どうしたらより良くなれるのか』と密にコミュニケーション取ることで自己や会社の成長を目指す倉庫です。最近は、それができ始めていることを実感していますし、数字にも表れていると評価しています」(石井さん)
進化し続けるドームいわきベース〜より機能的に、より効率的に業務を遂行するためのヒント〜
こうしたオペレーションは今後も適宜修正を加えていくつもりだと、石井さんは語ります。「最近だけでも、物流に求められることは大きく変化していきました。これから先もずっと同じオペレーションが最適だとは思っていません。改善に向けた取り組みを風通し良く、ドーム、ドームユナイテッド社がコミュニケーションを取りながらできるのが強みです。そして、既存の枠組みにとらわれることなく関係者全員が一丸となって、何が最適なのかを考え、取り組みを深化させることができているのを実感しています。顧客を起点とした4R(※)を実現するために、「スピード」、「コスト」、「品質」、3つのバランス、そしてそこにサステナビリティを適切に組み合わせる、この考え方を常に軸に据えて取り組んでいます」(石井さん)
(※)4R:Right Product, Right Place, Right Time, Right Quantity

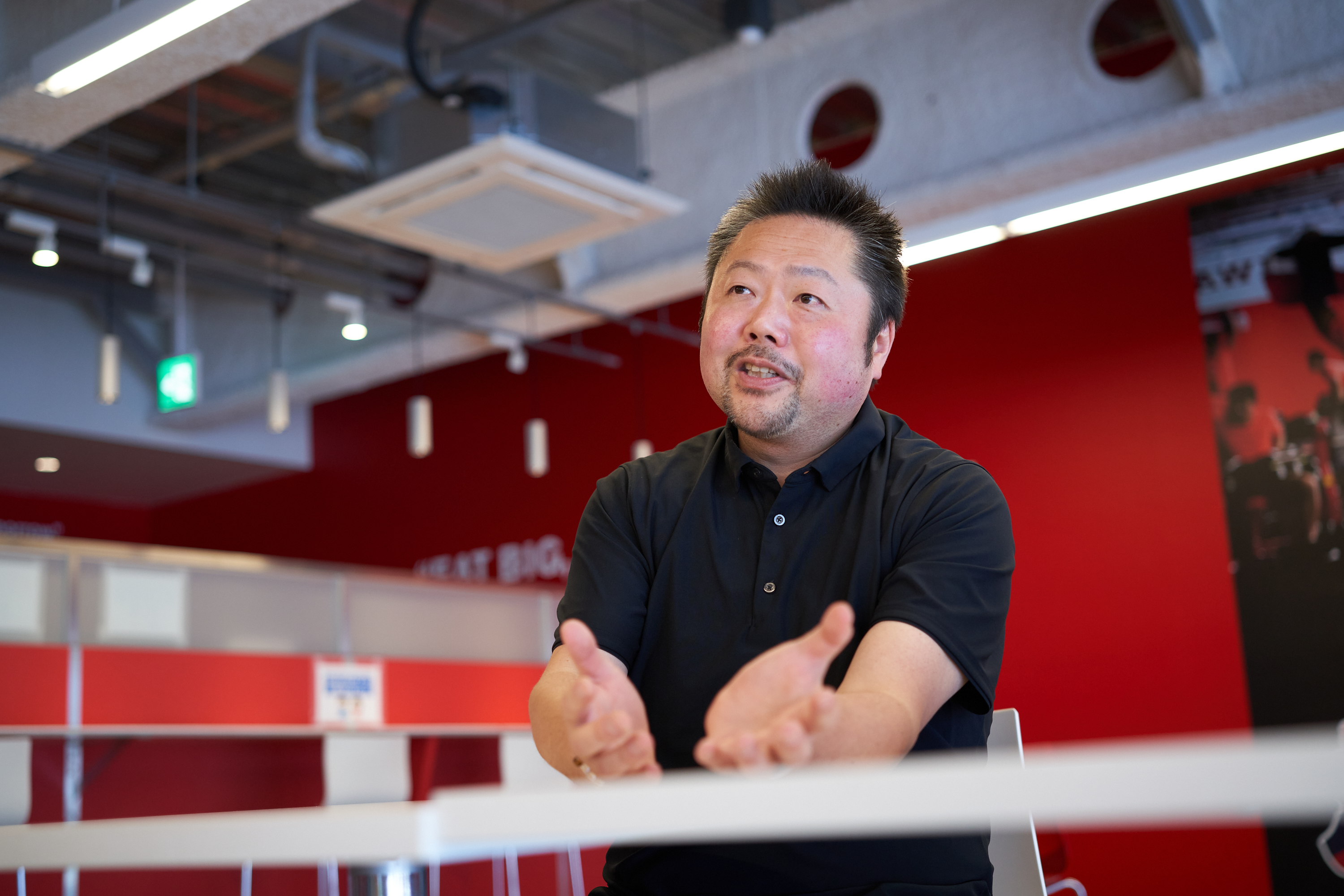
また、「倉庫の設立ストーリー、ブランドが生産性をさらにアップさせる」と石井さん。
「DIBは、スポーツを通じて世の中を豊かにし、震災からの復興と成長を目的とした『魂を息吹かせる倉庫』です。働いている人それぞれが、『扱っているのは自分たちのブランドだ』『カッコいいブランドの倉庫で働いている』と想えることは、生産性、モチベーション、働く意味では大切です。福利厚生や環境面も含めて、そうしたマインドをより高めていけるように取り組んでいこうと思っています」(石井さん)
緻密なデータ分析による予実管理と生産性向上のためのレイアウト設計、そして人の力によるモチベーション管理。これらを組み合わせることで、DIBの物流はさらなる進化を遂げていきます。