製品に欠陥があった場合に必要となる、回収業務。特に重大な事故につながる恐れがある場合は、法令の定めや自主判断によってリコールが行われます。
その際、製品の欠陥を軽視したり、リコールへの対応が遅れたりすることで社会的信用が失墜する可能性があるため、近年では誠実かつ迅速な対応が求められています。それは、製造物への責任も持つサプライヤーも同様です。リコールを招いた欠陥の原因が特定の部品だった場合は、その部品を供給しているサプライヤーも対応に追われるため、製品回収の流れや必要な物事をきちんと把握しておく必要があります。
リコール時のサプライヤーの責任やリスクに加え、迅速に対応するためのポイントを解説していきましょう。
サプライヤーにも問われるリコール発生時の責任・リスクとは?
製品に安全上の問題が生じるほどの欠陥が見つかった場合、法令の定めや自主判断で大規模な回収=リコールが行われます。 2020年には、経済産業省の管轄だけでも、1000件以上の重大製品事故が報告されました。
製造責任の視点からいえば、完成品(組立済の完成品)のリコールはメーカーの責任のもとで行われます。では、特定の部品が原因で完成品のリコールが行われた場合、その部品を供給しているサプライヤーには、どのような責任やリスクがあるでしょうか。
・法的責任
製造物責任法の範囲内になるため、製品の欠陥に起因する事故とそのために発生した損害について賠償責任を負うことになります。また、海外へ輸出されている製品の場合、日本国内の法律を超えた法的リスクを負う可能性もあるでしょう。
自動車や医薬品、食品など、製品ごとにリコール制度があるので法的責任の範囲は製品によって異なりますが、リコール命令に違反すると懲役や罰金、あるいはその両方を課される可能性があります。
・金銭的なリスク
リコール費用については最終製品製造業者であるメーカーがかぶることになります。
ただし、サプライヤーがメーカーからリコール費用やブランドイメージダウンなどについて賠償を求められることも。たとえば、ある部品を完成品に組み込む場合、その部品自体は安価でも、取り外しや交換作業が複雑になり、部品の単価をはるかに上回るコストがかかることがあります。その場合、サプライヤーに求められるリコール諸費用の負担額も、当該部品の売上高をはるかに上回る恐れがあるのです。
また、当該部品や材料が複数の製品に使われている場合にはリコール件数が増え、メーカーが負うリコール費用が増えるため、メーカーからサプライヤーへの損害賠償の額も大きくなるでしょう。
・社会的責任・リスク
安全性や品質に問題があるとして、業界内でブランドイメージを損ない、取引先を失う恐れがあります。
また近年は、メーカーとサプライヤーの2社による「リコール社告」となるケースが増加。リコール社告とは、製品の欠陥による影響を最小限に留めるために、会社名や製品名、回収・交換・修理などについて明確に変わりやすく記載した告知のことです。基本的には、最終製品製造業者であるメーカーが告知するものですが、「サプライヤーの責任も明記しておきたい」と考えて、サプライヤーの社名も記載する例が増えているのです。つまり、サプライヤーも世間の目にさらされ、責任を問われることになるので今後の事業に大きな影響を受ける可能性があります。
・業務負荷
リコールに伴う作業は膨大な量に及びます。
まず行うべきは、事実関係の把握です。製品の欠陥などが事故につながる可能性が高いかどうか、そしてユーザーの使用環境の変化などで事故などが起こる可能性がないかを調査・検討します。
そして、対策本部などの実施母体の設置も必要です。迅速かつ効率的に対応するためには、最高経営責任者などのもとに総務部長、開発部長、品質保証部長、製造部長、営業部長、カスタマーサービス部長、関係会社などがそれぞれの役割分担を果たし、対象となる製品の回収方法や修理方法、修理手順などを決めていきます。
そして、リコールがきちんと行われているか、どれくらいの割合で回収されているのかといった進捗状況のチェックも必要です。リコール状況を監視して、その成果を評価することが大事です。きちんと回収できないようであれば回収方法を再検討する必要もあります。あわせて関係機関、取引先、弁護士などとの情報共有も大切です。
また、特殊な修理・交換の場合は、専門家や熟練者を工場や営業所に派遣したり、作業者に研修・インストラクションなどを行ったりする必要があります。
こうしたイレギュラーな対応に追われ、作業員が不足したり、メイン工程に遅れが生じたりする可能性は低くありません。
リコール発生時の「メーカー」と「サプライヤー」の対処手順とポイント
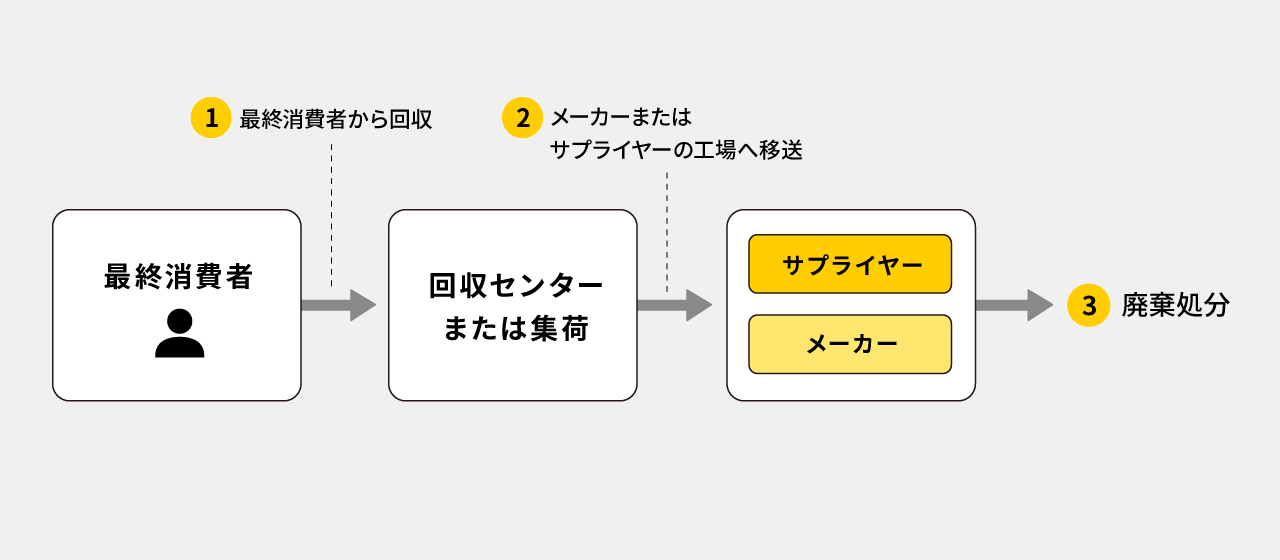
<廃棄処分の場合>
1. 最終消費者から回収
2. メーカーまたはサプライヤーの工場に移送
3. 廃棄処分
リコールがかかった製品は、販売店や営業所などに併設された回収センターで回収、または消費者から集荷します(メーカーにダイレクトに戻る場合もあり)。
修理・交換対応ではない場合は、回収センターまたは、製造各社の工場から廃棄処分に回します。
ここで発生するリコール費用(輸送コスト、廃棄処分コストなど)は2通りのどちらかのパターンで処理されることが多いです。
・メーカーが負担して、その全額、あるいは必要分をサプライヤーに請求
・サプライヤーが負担して、そのうちの一部、あるいは全額をメーカーが負担
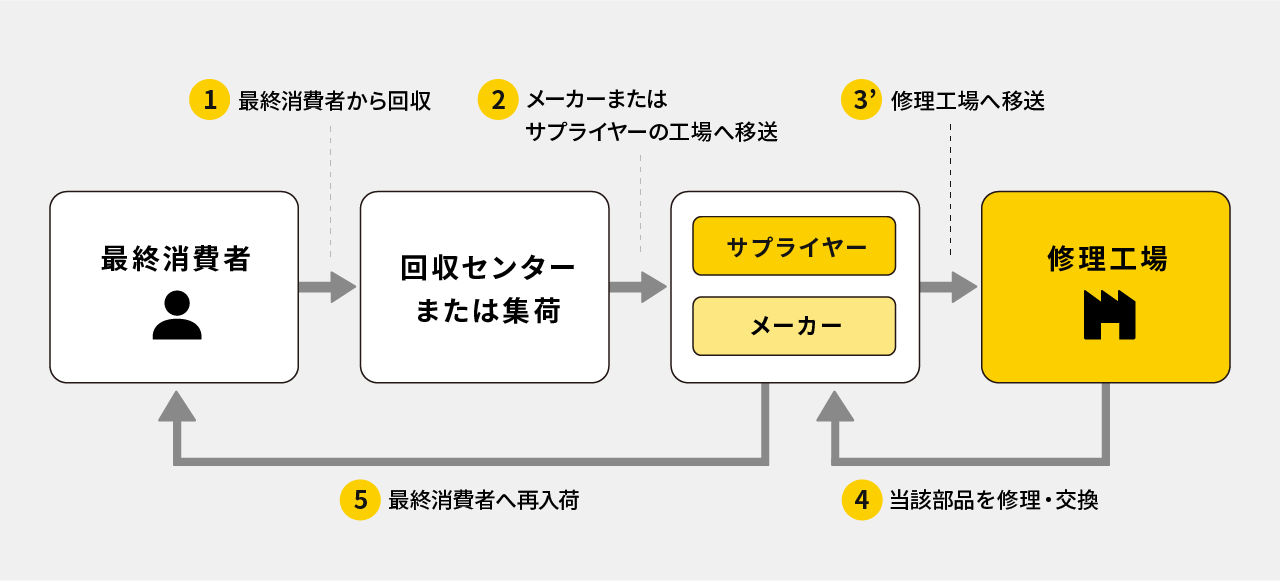
<修理・交換の場合>
1. 最終消費者から回収
2. メーカーまたはサプライヤーの工場に移送
3. 修理工場となる、メーカーの契約工場やサプライヤーの工場に移送
4. 当該部品の修理・交換を行う
5. 最終消費者へ再出荷
部品自体の修理・交換な場合は、販売店や営業所などに併設された回収センターで回収、または消費者から集荷後に、サプライヤーの工場で修理を行い、メーカーの工場で製品に再度組み込みます。
ここで発生するリコール費用(修理・交換・輸送コストなど)は、廃棄の場合と同じように、2通りのどちらかのパターンで処理されることが多いです。
・メーカーが負担して、その全額、あるいは必要分をサプライヤーに請求
・サプライヤーが負担して、そのうちの一部、あるいは全額をメーカーが負担
こうした流れに伴って、さらに消費者への返金についても考えておく必要があります。多くの場合、次のような流れで支払いが行われます。
・メーカーから(返金)最終消費者へ返金
・サプライヤーからメーカーへ賠償請求支払い
また、最終消費者に何らかの補償金が必要な場合は、メーカーあるいはサプライヤーから支払われるかたちがとられます。また損害賠償などは裁判などを経てサプライヤー、あるいはメーカーから最終消費者に支払われます。
リコールの業務負荷への対処法は?
こうした回収物流のフローの中で留意すべき点としては、「非常に多くの量を短期間に回収することが要求されているにもかかわらず、実際は回収に時間がかかる、修理や交換を迅速に行えない」「製品が戻ってくるタイミングがメーカー依存になり、サプライヤーが把握できない」「大量の回収製品の修理・交換、廃棄などの作業がメーカー都合のタイミングとなり、自社の通常生産ラインを圧迫する」といったことが挙げられます。
対処法は次の通りです。
・回収ネットワークを整備する
・修理や交換が必要な場合は、契約工場数を十分に確保して、修理ラインを設ける
・回収にあたっての手順や段取りを組織内で周知させ、十分な人員を用意して対応する
回収の段取りをきちんと把握して人員を確保するなど、ネットワークの整備が基本となります。1製品あたりの修理時間を細かく把握して、そこから必要な人員や期間を細かく割り出し、全体の見通しを立てるようにしましょう。
一方で、通常の生産ラインへの負荷を考えると、流通加工業務に慣れた作業スタッフを抱えている物流センターを利用することも検討するべきです。回収から修理・交換、再出荷のすべてを物流会社に任せることで、業務負荷を軽減させることが可能です。
準備は万全ですか?サプライヤーが取るべきリコール対応実践チェックシート
リコール対応をスムーズに行うためには事前の準備や心構えが重要です。今一度、自社の備えをチェックしておきましょう。
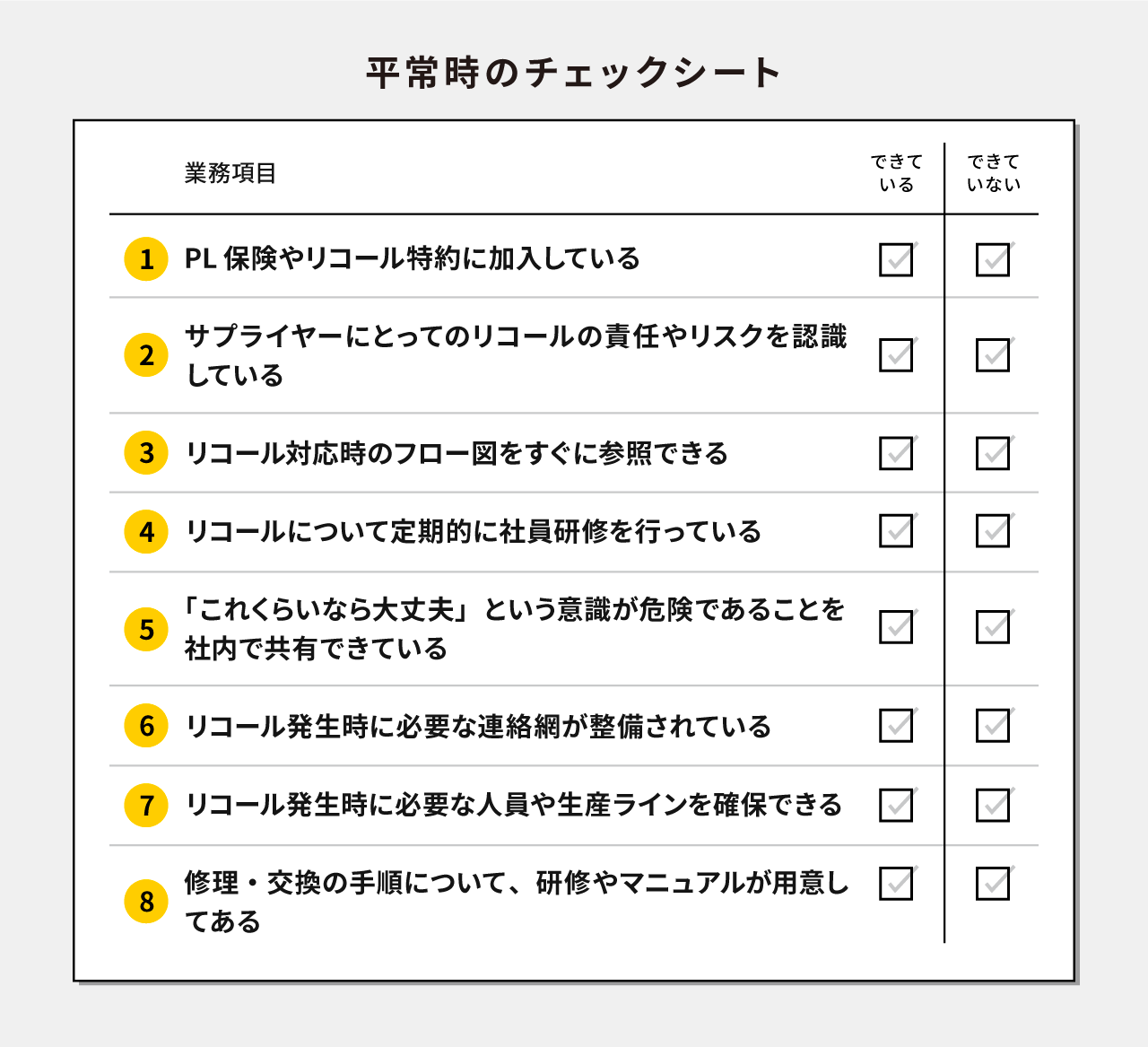
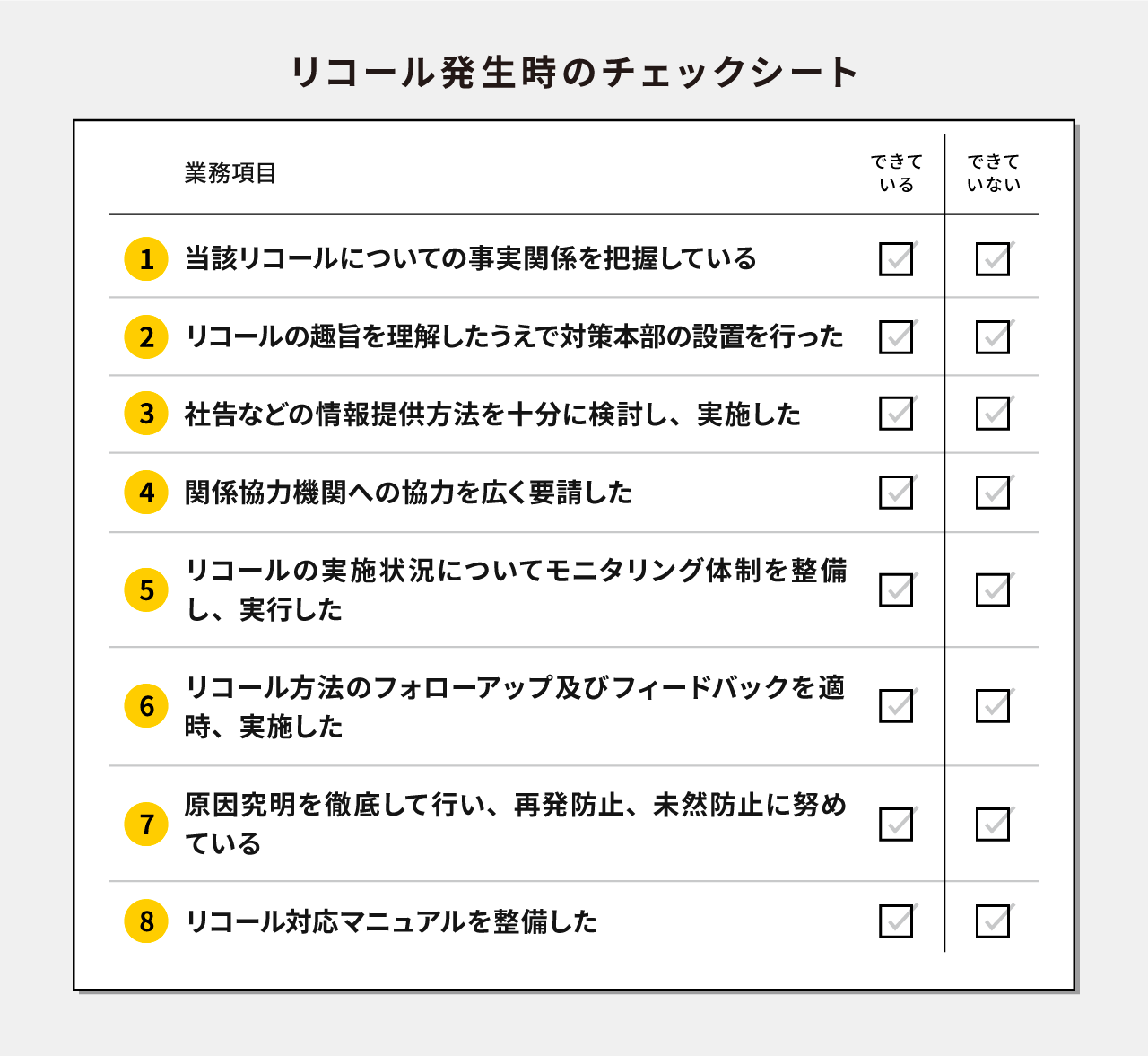
ただでさえイレギュラーな業務でありながら迅速さも求められるリコール対応。自社製品の欠陥が消費者に与える被害や今後の事業への影響を最小限にとどめるには、回収から修理・交換のフローをいかに滞りなく、スムーズに行えるかが肝心です。
そもそも欠陥や問題のない製造を心がけるのは大前提として、もしものリコール発生にも十分な準備をしておきましょう。
監修:鈴木 邦成(すずき くにのり)※掲載記事の内容は監修当時のものです。
物流エコノミスト、日本大学教授(在庫・物流管理など担当)。博士(工学)(日本大学)。
早稲田大学大学院修士課程修了。日本ロジスティクスシステム学会理事、日本SCM協会専務理事、日本卸売学会理事、日本物流不動産学研究所アカデミックチェア。ユーピーアールの社外監査役も務める。専門は、物流・ロジスティクス工学。